Many iconic buildings demonstrate the most interesting or unique designs that modern engineers can create for their various clients. But at Toronto’s York University, the new Bergeron Centre for Engineering Excellence stands out as a singular structure that was designed by engineers, for engineers—specifically, the students in the university’s Lassonde School of Engineering. The Lassonde School is relatively new, having been established in November 2011, and the Bergeron Centre is even more recent. The C$113-million (U.S.$85.6-million) project was completed by September 2015 and opened officially in April. It was named in recognition of alumnus Douglas Bergeron and his wife, Sandra, who were major donors to the project.
Housing York University’s civil engineering program, along with the mechanical and electrical engineering disciplines, the 16,000 m² structure features five concrete-framed levels above grade and a steel-framed penthouse for mechanical systems on the roof. The single basement level extends beyond the building’s footprint and, given the slope of the site, is partially aboveground.
Intended for what the university calls “renaissance engineers,” the Bergeron Centre was “designed with a student-centric philosophy in mind that challenges the look of a traditional engineering school,” explains the York University website. “The structure’s unique architectural design reflects its main purpose—[being] a hub for entrepreneurship, collaboration, and creativity.” In line with that philosophy, the building features 18 teaching labs—including a triple-height facility for structural engineering known as the High Bay Lab, which is isolated from the rest of the structure—and 8 so-called active learning labs, where students will work in groups. But there are no traditional lecture halls; nor are there classrooms with seats and desks bolted to the floor in straight lines. Instead, the spaces feature movable chairs that can be arranged around movable desks to create settings that feature technology for students to plug in their laptops or other devices so they can work interactively and collaboratively.
The main portion of the new building is an irregular oval in plan that features multiple radii. It is wreathed in a multifaceted cladding formed from some 10,000 triangles made of either glass or composite aluminum panels that were designed with the assistance of a mathematician to create a seemingly nonrepetitive pattern. An intricate steel framework was connected to the building’s concrete floor slabs to support the cladding, which is held out from the perimeter of the building and suspended above the ground-floor level. Because the building had to be completed in time for the fall 2015 semester, the glass for the windows was being fabricated at the same time that the steel frames were being installed.
THE MAIN PORTION OF THE NEW BUILDING IS AN IRREGULAR OVAL IN PLAN THAT FEATURES MULTIPLE RADII.
The Bergeron Centre was designed by Toronto-based architecture firm ZAS. The Toronto office of the international engineering firm Arup provided structural, civil, and mechanical and electrical engineering services for the project, as well as information technology, communications, and security consulting. The Toronto office of Blackwell Structural Engineers was responsible for the engineering design of the faceted facade and building envelope, in particular, the steel frames that support the triangular glass and aluminum panels. The Toronto office of the Flynn Group of Companies was the building envelope contractor and carried out the design of the panels themselves.
The Markham, Ontario, office of exp was the project’s geotechnical engineer. Toronto-based mesh Consultants, Inc., provided the mathematical analysis that helped produce the triangular pattern, and Scott Torrance Landscape Architect, also of Toronto, was responsible for the landscape architecture. The Toronto office of the international firm Laing O’Rourke and Toronto-based Gillam Group, Inc., formed the construction management team.
Two aspects of the natural world—clouds and rocks—inspired the building’s aesthetics, notes the ZAS website. The cloud metaphor is evoked by the multifaceted facade, while the rock imagery is seen both in a particular portion of the building’s roof—the part above a workshop in the basement extension—and in the structure’s overall surroundings. As the ZAS website explains: “With a university mandate to create a world-class facility, the building was conceptualized as one that is rooted like a ‘rock’ in the landscape of the campus and yet limitless like a ‘cloud.’… Particularly notable is the unique facade of the cloud panels on the upper levels of the building where a scale-less aesthetic of tessellated glass and aluminum panels [is] unlike any other on campus. Its shimmering pattern of materials and reflectivity are always changing, much like the students’ work that will be created within it.”
The Bergeron Centre building was constructed on a previously open site encompassing roughly 3 ha between other campus buildings that had been used primarily for surface parking and as vegetated space, says Peter Preston, P.Eng., Arup’s senior civil engineer on the project. The site slopes from north to south toward an existing stormwater management facility known as Stong Pond, an open body of water that already accommodates its maximum capacity. “So we couldn’t increase any peak flows to it from any new development,” Preston says.
To manage the potential increase in runoff generated by the Bergeron Centre, the project included a system of two dry ponds placed in series upstream of Stong Pond to offset the timing of peak stormwater flows from different areas of the site. The dry ponds are essentially excavated bowls, one with a capacity of 250 m³ southeast of the new building and the other with a capacity of 1,450 m³ to the southwest. The two will fill with water only during a storm to provide temporary attenuation and help manage the eventual release of the stormwater to Stong Pond, Preston explains.
Because of the relatively low infiltration properties of the soil at the project site, an underground chamber also was constructed to facilitate the entrance of stormwater into the ground. Featuring a high void modular structure resembling stacked milk crates and wrapped in both clear stones and geotextiles, the underground infiltration chamber was constructed along the southwestern edge of the site. When combined with the vegetated roof systems that were constructed on the building, these various stormwater measures helped the project reduce the rate and volume of stormwater runoff at the site by at least 25 percent while also improving the capacity of Stong Pond, notes Preston.
Two deep storm and sanitary trunk sewers, each about 525 mm in diameter and located as much as 11 m below grade, had to be relocated because they would have been directly beneath the new building, preventing manhole access and conflicting with the new building’s foundations, Preston says.
Varying soil conditions across the site led to the use of different foundation systems, depending on the location, notes Walid Elsayed, Ph.D., P.Eng., an Arup structural engineer. These included concrete caissons 900 mm in diameter that ranged in length from 5 m to 8 m, 400 mm diameter micropiles 10 m deep, and spread footings. A history of floods at the site raised concerns about possible water infiltration into the building, especially in some of the laboratories, including the High Bay Lab, housing equipment highly sensitive to moisture, Elsayed says. These laboratory spaces were sealed to prevent leaks by using a special type of concrete containing a crystalline admixture that, when exposed to water, forms a crystal that expands to fill the gaps and prevent any water penetration, Elsayed explains.
The floor and walls of the High Bay Lab are structurally isolated from the surrounding building to minimize the transmission of any vibrations during the “noisy, destructive types of testing” performed in the lab, making it “like a building within a building,” Elsayed says. Measuring 20 m square in plan and 13 m tall, the High Bay Lab extends down to the basement level and features a separate foundation system composed of spread footings. The lab’s 300 mm thick reinforced-concrete walls perform a double function, serving as load-bearing walls to support the structural system and acting as insulation between the lab and the adjacent rooms and classrooms, Elsayed says.
Within the High Bay Lab is a 1 m thick floor at grade, known as the strong floor, and a so-called strong wall that is L shaped in plan and measures 1.5 m thick and 6 m tall. Both the strong wall and the strong floor are perforated with a grid of anchor points installed 600 mm apart on center that are used during lab tests. The lab uses hydraulic and other specialized equipment to test prototype structural elements and construction materials to the point of destruction.
The ceiling of the High Bay Lab is not structurally connected to the laboratory’s walls. Instead, this 300 mm thick concrete slab features 1 m deep steel girders that span the lab space in the east–west direction and rest on composite columns that are located outside of the laboratory’s footprint. The High Bay Lab itself required a column-free space, Elsayed explains, so the unconnected ceiling supports building columns above the laboratory that could not be extended down into the lab. The thick slab helps to provide noise insulation. The ceiling also incorporates an overhead crane with a capacity of 12.5 tons.
The distinctive triangles of the Bergeron Centre’s facade include both aluminum panels and glazed windows, the latter arranged generally in clusters of anywhere from 2 to 16 triangles. Although the concrete building itself curves in plan, the steel framework features a series of straight elements that bend to create the illusion of curving, each panel featuring two to four bends, explains Shannon Hilchie, P.Eng., who served as a consultant to Blackwell Structural Engineers for the design of the steel frames that support the cladding. To ensure that they could be transported to the site on regular trucks, the maximum height of the frames was set at 3.66 m, she adds.
The thousands of triangles on the facade were actually formed from just three basic shapes developed by the mesh mathematician, says Hilchie, while the frames were created from 165 unique prefabricated hollow structural section elements. The frames are set 500 mm out from the concrete edge of the Bergeron Centre building to accommodate two layers of insulation between the cladding and the concrete structure and are anchored to steel plates embedded in the floor slabs.
The seemingly nonrepetitive design of the triangles “actually does repeat, but it repeats in a way that to the human eye doesn’t look like a pattern,” notes Svetan Veliov, P.Eng., an Arup electrical engineer who was responsible for the mechanical, electrical, and plumbing systems in the Bergeron Centre. A person can “stare at this building for quite a while trying to find the pattern, and it’s almost impossible,” Veliov adds.
A series of pin connections, four per frame, were used to secure most of the frames to the building. In certain locations at the top and bottom of the system, where the frames are not full sized, moment-resisting connections also were used. Although pin connections can normally accommodate tolerances of half an inch or so, in this project the tolerances were much tighter, a mere 3.2 mm, Hilchie says. Thus, “we had to anticipate any tolerance issues…. We needed to allow [the frames] to move up, down, side to side, and also have one side move up and one side move down independently” with an accuracy that was “almost unheard of in construction,” she notes.
Roughly 1,000 of the 10,000 triangles are glazed panels, which were combined in clusters to accommodate the project’s schedule and avoid the more time-consuming approach of putting in the glass panels one at a time, says Noel Cunningham, the Flynn Group’s construction manager for glazing. Flynn employees worked directly with the mesh mathematician to resolve constructability issues as well as such technical aspects as how to make the panels airtight and watertight, Cunningham explains.
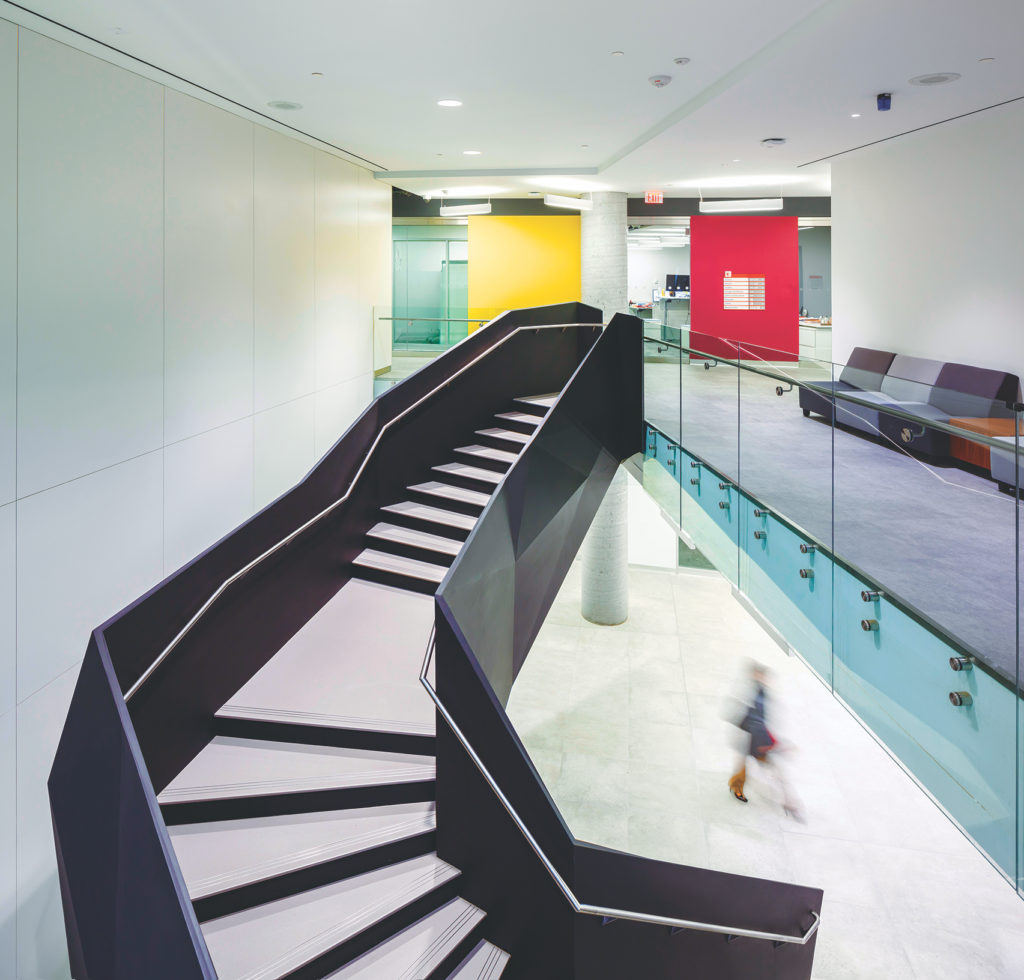
Modifying existing technology to meet the specific requirements of the Bergeron Centre project, Flynn developed a custom system made from aluminum plates for the opaque panels, as well as systems for the glazed sections, says Michael Roche, the company’s manager of business development for North America. Three-dimensional printing was used to produce full-sized profiles of the new systems to show the design to the architect, Roche says, and laser scanning was used to carefully position the panels on-site. “We adjusted the glass clusters around until they hit the laser points, and then we knew they were in the right position,” Cunningham says.
Each of the glazed clusters contained multiples of the three triangle sizes, Roche says, and as the frames and panels followed the various curves and radii of the concrete building, the systems had to be repeatedly adjusted. “While the triangles remain the same size,” Cunningham explains, “their relationship to each other changes.”
The appearance of the aluminum panels also changes slightly around the building. The different angles create changing shadows, and different paints alter the colors of the cladding.
Because of the tight schedules, Blackwell also tried a new approach to organizing contract documents. Instead of following the traditional practice of providing the steel fabricator with a document that simply described each piece of steel, having the steel fabricator then make its own models of how to cut that steel, and then having the engineer review the model, Blackwell decided to “own that portion of the work,” Hilchie says. This effort, which represented approximately 90 percent of the shop drawings, involved having Blackwell produce the models for each piece of steel. Then the fabricator—Norak Steel Construction Ltd., of Concorde, Ontario—used Blackwell’s models to cut the elements precisely. It was “something we’d never done before and something that engineers don’t normally do,” Hilchie says, but it was an innovation that saved considerable time and expense.
Of course, the project deadlines also gave Hilchie some frantic moments as she tried to create those models of the frames within six weeks, especially after taking fully half that time to create the model for just the first panel. Designing the frames using SolidWorks software—from Dassault Systèmes SolidWorks Corporation, of Waltham, Massachusetts—Hilchie found herself focusing on the project everywhere she went, thinking about it in her car, working on it when commuting on a train, even “getting up in the middle of the night trying to do it!”
THE AESTHETIC CHARACTERISTICS OF THE VEGETATED ROOF OF THE WORKSHOP AREA SUGGEST A ROCKY TERRAIN, iN KEEPING WITH THE ROCK METAPHOR CREATED VIA SHEETS OF INSULATION SHAPED INTO THE GEOLOGICAL FORMS.
Fortunately, the second panel took just two days to complete, and the rest came even more quickly. This was because, although she hadn’t realized it at the time, the first two panels had involved “most of the problems I could anticipate,” Hilchie says. Thus, by the fourth panel, “I had experienced pretty much every problem I could come across and so had a solution.”
In the end, Hilchie was able to provide the steel fabricator with the models for the first batch of panels at the four-week mark, which allowed the fabrication process to start a little early. Ultimately, just two panels out of the entire system ended up having a problem, she adds, which resulted in just a few hours of work in a shop to fix, in contrast to what could have been a week of lost construction time under a more traditional approach.
The aboveground portion of the Bergeron Centre’s basement level, which, as mentioned previously, extends beyond the building’s footprint, is located on the southern side of the site. It includes workshops that open via garage-style doors onto an open-air site known as Innovation Plaza. The aesthetic characteristics of the vegetated roof of the workshop area suggest a rocky terrain—in keeping with the rock metaphor—created via sheets of insulation shaped into the geological forms, says Elsayed.
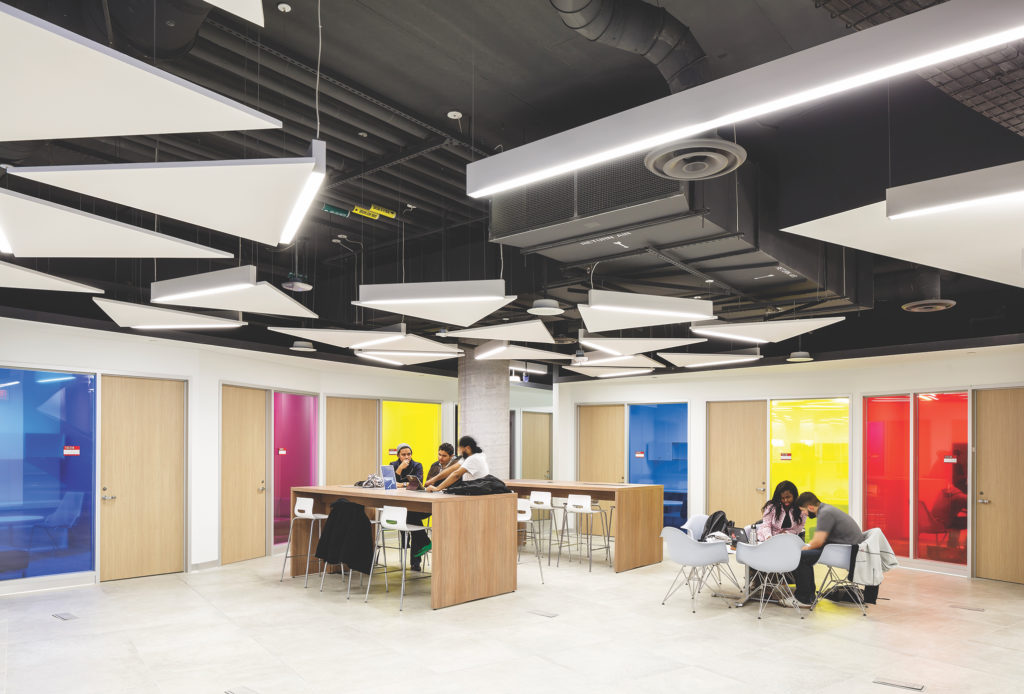
Because other portions of the basement are located underground and thus have no windows, the green roof above the workshops also features a series of “solar tubes,” essentially tubular skylights roughly 2 to 3 m in length designed to enable natural daylight to reach deep into the basement level, Elsayed explains.
On the east side of the Bergeron Centre, a basement-level tunnel extends from the new engineering building to the adjoining Scott Library, where an opening had to be cut into the library’s basement, says Elsayed. An expansion joint separates the tunnel structurally from the library building, he adds.
Providing access between the ground floor and the second level of the Bergeron Centre is a large semicircular staircase that is attached at the top and bottom but features no intermediate supports. Framed in steel, the roughly 16 m long stair presented vibration challenges because of its length and curving form, says Elsayed. So two thin steel beams were attached between the back side of the stair and the adjoining wall, creating a lateral connection that does not accommodate any of the gravity loads but does control the vibration, he says.
THE THOUSANDS OF TRIANGLES ON THE FACADE WERE ACTUALLY FORMED FROM JUST THREE BASIC SHAPES DEVELOPED BY THE MESH MATHEMATICIAN, WHILE THE FRAMES WERE CREATED FROM 165 UNIQUE PREFABRICATED HOLLOW STRUCTURAL SECTION ELEMENTS.
The mechanical systems for the building are primarily located in a partially enclosed rooftop structure, thus freeing more space in the basement level for classrooms and laboratories, notes Veliov. Designed so that the “entire building is geared toward energy efficiency,” Veliov says, the Bergeron Centre is considered likely to earn gold certification in the U.S. Green Building Council’s Leadership in Energy and Environmental Design (leed) program. In this respect, Veliov points to the use of high-efficiency fans in the laboratory exhaust systems, along with such features as a radiant heating system, a rooftop chiller, and the use of both light-emitting diode fixtures and fluorescent lights to maximize efficiency. There is also a demand-response ventilation system that utilizes air-side economizers that will potentially capture 50 percent of the energy that would otherwise be lost from heating or cooling air exhausted from the building.
On a hot summer day, for instance, “the indoor air gets exhausted, which is nice cool air, and then you suck in hot, humid air,” Veliov says. “So the air-side economizers exchange that energy so that the air leaving the building helps cool the air coming into the building.”
The fact that the Bergeron Centre is a building used by engineering students resonated with many members of the design team. “Geometrically it was one of the most interesting buildings I’ve worked on,” Veliov notes, “but it was also special because it was an engineering building, so we coined the phrase ‘The engineering building designed by engineers, for engineers.’”
Having spent “quite a significant time” of his life in structural labs earning his own postgraduate degrees in civil engineering, Elsayed says he used that experience “to facilitate the design to make it easier for the students to use the space conveniently…. I enjoyed doing that because I know what is vital to use and what is the function of the building because I was living in that environment.” In the application by Arup for the Consulting Engineers of Ontario’s2016 awards program—in which the Bergeron Centre was named one of the winners of the Award of Merit—Janusz Kozinski, Ph.D., P.Eng., the founding dean of the Lassonde School of Engineering, was quoted as saying that York University seeks “to create engineers who are ‘rational, ingenious, passionate, confident, and creative,’ who will ultimately contribute to the greater good of society.”
If the setting for such an education plays any role, then the university’s new engineering building ought to give those Lassonde students a good start.
This article first appeared in the November 2016 issue of Civil Engineering.
PROJECT CREDITS Client: Lassonde School of Engineering, York University Architect: ZAS, Toronto Structural, civil, and mechanical and electrical engineering, information technology, communications, and security consulting: Arup, Toronto office Facade and building envelope design: Blackwell Structural Engineers, Toronto office Building envelope contractor: Flynn Group of Companies, Toronto office Geotechnical engineer: exp, Markham, Ontario, office Mathematical consultant: MESH Consultants, Inc., Toronto Landscape architect: Scott Torrance Landscape Architect, Toronto Construction management: Laing O’Rourke, Toronto office, and Gillam Group, Inc., Toronto