The new Kosciuszko Bridge, also known as the K Bridge, is a twin-span, cable-stayed structure that traverses Newtown Creek, linking the New York City boroughs of Brooklyn and Queens via the Brooklyn–Queens Expressway, which runs east to west. Built in two phases, the eastbound bridge was completed in April 2017, and the westbound bridge was completed in August 2019. Both phases represent the first major bridge in New York City since the Verrazano–Narrows Bridge in 1964, and it is the state’s first cable-stayed bridge.
The existing bridge, opened to traffic in 1939, was a through-truss crossing that comprised six narrow travel lanes, three in each direction, with no shoulders. Designed to carry just 10,000 vehicles per day, by the time it was replaced, the volume was nearly 18 times that number. Because it was a main transportation gateway between Brooklyn and Queens, replacing it was the only option. After considering several designs, in 2009 the New York State Department of Transportation (NYSDOT) selected a twin, cable-stayed bridge—an option that meant longer span lengths and ideal aesthetics.
In 2014, the Skanska USA–Kiewit Corp.–ECCO III Enterprises Inc. (SKE) joint venture was formed, with HNTB Corp. serving as the design-build team’s lead designer for the replacement of the eastbound side of the bridge in phase 1. The $555-million phase 1 project was comprehensive. It not only included the construction of the 1,100 ft long, single-tower eastbound span but also the construction of high-level approach bridges, low-level connectors with numerous overpasses over local streets, and the demolition of the existing structure. Phase 2 was completed as a design-bid-build, best-value project. WSP USA designed and Granite Construction Northeast Inc. built the phase 2 project.
—Jim Peterson, P.E., DBIA
Going East: Brooklyn to Queens
Determining how to replace the heavily trafficked eastbound span and all its approaches was a complex conundrum, one which HNTB simplified by reworking the off-alignment approaches. “It was a complicated problem that we solved with a simple answer,” says Hans Hutton, P.E., S.E., a vice president of HNTB and the chief bridge engineer for phase 1. “That’s the true beauty of the project.”
“Micropiles were used to advance an accelerated bridge construction approach to the Morgan Avenue crossing on the Brooklyn side of the new bridge,” says Matthew Riegel, P.E., D.GE, M.ASCE, an HNTB fellow, vice president, and geotechnical team leader. He also served as the foundation engineer of record for the project.
Staged fill embankments retained by 40 ft high prefabricated modular retaining walls, or T walls, were also deployed during construction. The team built approximately 2,000 ft of earth-filled embankments beneath the existing, in-service, column-supported Brooklyn–Queens Expressway viaduct. The existing structure could tolerate only minimal differential settlement because of its stiffness, so it was reinforced with fiber wrap and carefully monitored for movement during fill placement.
“Construction beneath the existing Brooklyn–Queens Expressway, which is supported on shallow foundations, presented some unique design and construction challenges associated with work in low-overhead conditions and potential impacts to the existing structure,” Riegel says. “Because the design-build team elected to use normal earth fill rather than lightweight fill, it was up to the designer to evaluate impacts and prove that this approach could work safely with the adjacent in-service structure.”
Geotechnical assessment of the soils supporting the existing expressway was a critical aspect of this design because soil behavior when subjected to additional stress could drive settlement and the potential deformation of the in-service viaduct. HNTB conducted significant structural analyses to ensure the existing bridge would be stable and structurally sound as crews constructed the embankment below it and dismantled the viaduct in stages. It remained stable throughout the project.
The availability of property below the bridge dictated the foundation locations and span arrangement, which is highly asymmetrical. The main span length is 624 ft long and the back span is 377 ft long. Because the main span is significantly longer than the back span, the potential for uplift at the west anchor pier was high. This dynamic would cause it to be lifted like an unbalanced seesaw. This difficulty is not uncommon and has been addressed in a variety of ways on other projects. One way is to provide continuity between the back span and the approach spans so that the approach spans add to the weight of the back span. This solution, while helping solve the uplift problem, would have created several other challenges on the K Bridge.
HNTB’s solution was to install a counterweight to the end of the back span. At the western end of the back span near the anchor pier, the space below the deck and between the edge girders was filled with heavyweight concrete. This increased the weight of the back span and balanced the seesaw—a simple solution that did not add complexity to the bridge.
One issue encountered during the design was that the existing Brooklyn approach viaduct and the new Brooklyn connector would occupy nearly the same space, having the same elevation and a similar alignment. The team’s solution was to design a “viaduct-in-kind”—that is, one lane at a time while traffic continued to flow, also known as a replace-in-place concept. HNTB and SKE opted to first move traffic to the far-left side of the original span while the far-right lane was deconstructed. The process was then repeated, switching sides, to deconstruct and build the new viaduct one lane at a time. That ingenuity meant the team did not have to build a 1 mi temporary bridge to serve traffic while the new bridge was being built, saving time and money.
Once the eastbound span was in place, the old bridge was demolished using linear-shaped charges, which dropped it to the ground adjacent to the new bridge. “Projected vibration levels were checked by HNTB to ensure the new bridge was adequately protected during this operation. Cushions of soil and steel plate were designed and installed on the ground surface to absorb the vibration, keeping adjacent buildings and the new eastbound bridge safe from damage,” said Jessica Miller, P.E., the assistant project manager for SKE and a project manager for Skanska.
Using linear-shaped charges in the demolition of old bridges has grown in popularity over the past few years. The charges implode the bridge, cutting it at critical support points to weaken it and ultimately cause failure via collapse, according to Miller. This creates smaller pieces that can be cut further once they are on the ground for transport as scrap metal, as was the case with this project’s main span. This method is safer and more economical than cutting a bridge apart in place, which requires significant aboveground labor.
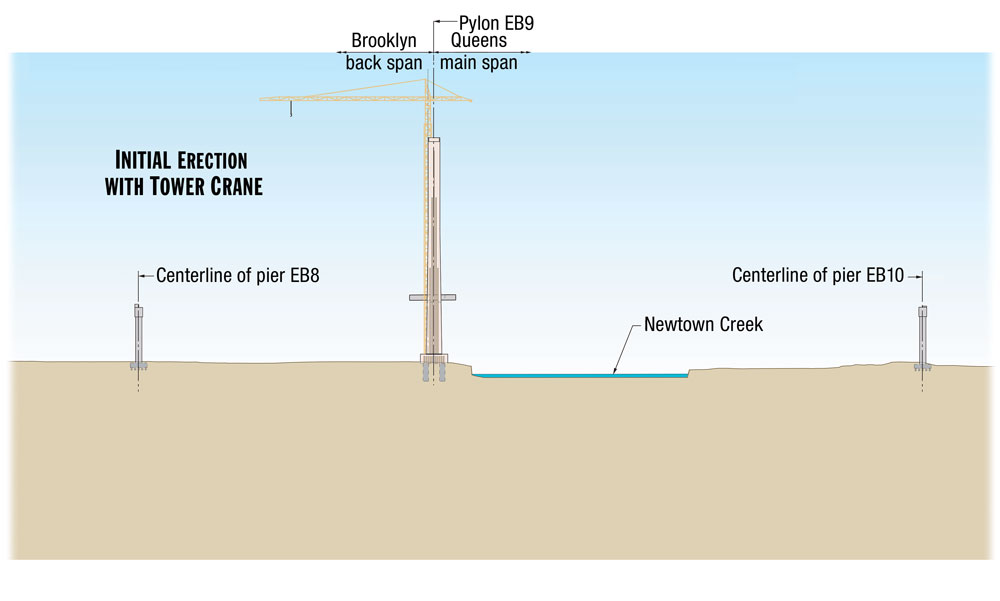
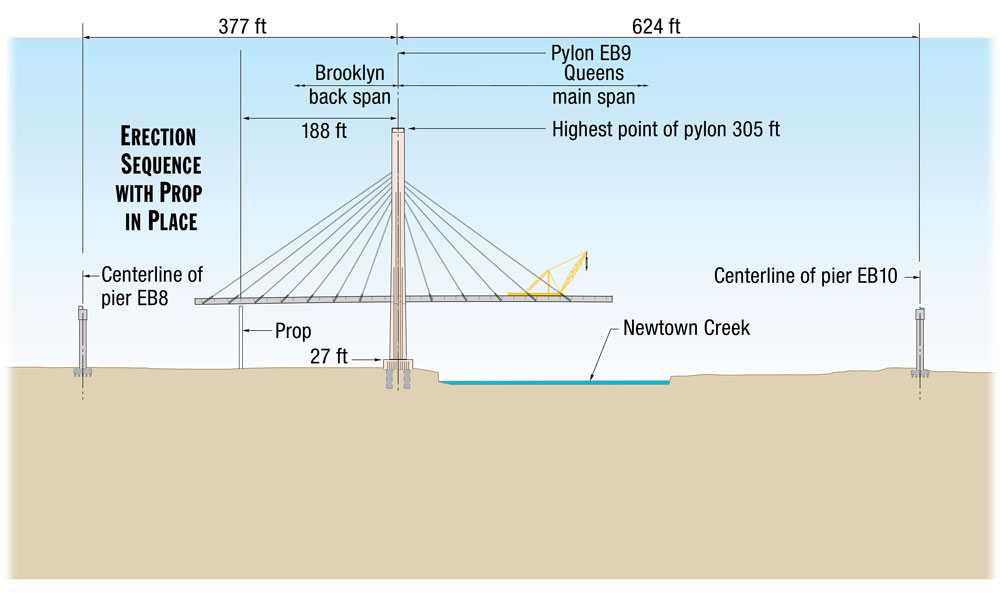
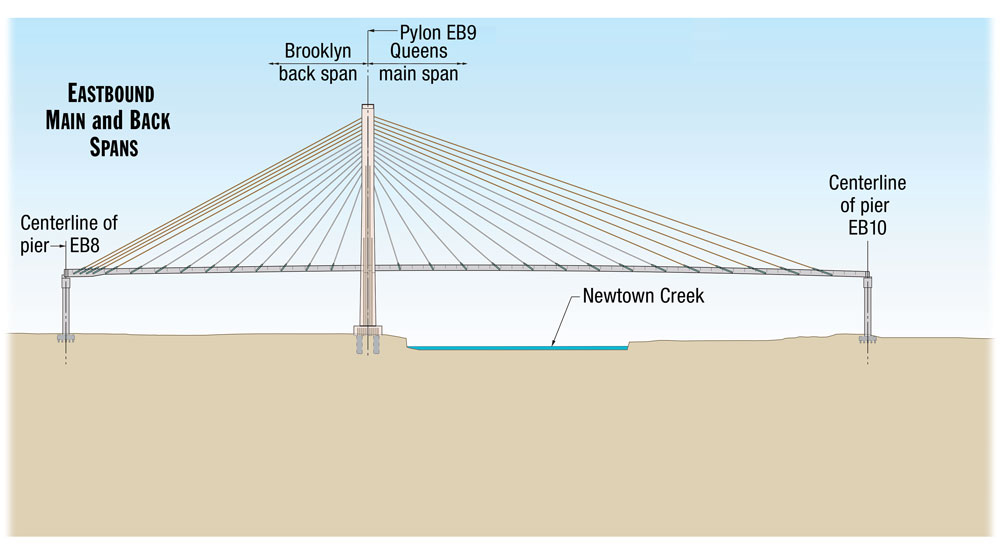
The asymmetry of the new cable-stayed bridge also presented challenges during its erection. Both the main and back spans are composed of segments that are spliced together, and the splices are located near the point where the cables attach to the superstructure. The segments in the back span are about 31 ft long, and the segments in the main span are about 41 ft long. These types of bridges are typically built using balanced cantilever erection; the first segment is set at the pylon and suspended by stay cables. Next, one field segment is installed in either the back span or the main span, which causes an imbalance about the pylon. Then another segment is installed in the opposite span to restore balance.
In a symmetrical bridge, the maximum imbalance would be that of one segment. Given the difference in segment lengths for the K Bridge, the imbalance would continue to grow toward the main span if a modification was not made to the method, so additional segments were installed in the back span to minimize imbalance during erection. A detailed erection analysis examined these issues and was used to obtain the locked-in dead load of the superstructure.
An interesting design aspect of the new K Bridge is that it is lower than its predecessor, which is rare in modern construction and engineering. “The old bridge was designed for larger navigational clearances than the new bridge,” which was problematic, Hutton says.
The approach grades were steeper on the existing bridge because of its height, and trucks had trouble maintaining their speed. The new bridge solves that problem.
Because the bridge’s piers and pylons are onshore, designers did not have to take ship impacts into consideration in their design.
Another achievement of the K Bridge replacement was the compressed design schedule.
Another achievement of the Kosciuszko Bridge replacement was the compressed design schedule. SKE planned the installation of the main span’s drilled shafts in October 2014, and in the meantime HNTB began the final bridge design. Within five months, HNTB had conducted wind testing, performed a nonlinear-time history analysis, progressed the entire bridge design to the 20 percent level, and finished designing the bridge foundations to meet the compact schedule.
For a cable-stayed bridge, that compressed schedule is the epitome of accelerated, Hutton says. It was only through constant communication among SKE, HNTB, and NYSDOT that the schedule was met. At the time, the replacement of the eastbound side of the bridge was the largest design-build project ever awarded by the NYSDOT and the first major design-build project in the five-borough region.
The eastbound bridge was constructed parallel to and on the eastbound side of the original structure and initially carried both eastbound and westbound traffic until the westbound span opened in August 2019.
Until the design-build contract was awarded to HNTB and SKE, NYSDOT had planned to deliver the project under a series of four smaller design-bid-build contracts, with a completion date of 2024. Using design-build allowed the department to save three to four years on the overall project completion. The Kosciuszko Bridge project is proof that a project such as this can move from a traditional design-bid-build best-value delivery method to design-build as the project develops, with great success.
—Jim Peterson, P.E., DBIA
Going West: Queens to Brooklyn
The westbound span of the Kosciuszko Bridge, opened to motorists, cyclists, and pedestrians on August 28, 2019, is the most recently completed piece of the multiphase NYSDOT Kosciuszko Bridge project.
Delivered under a design-bid-build contract, this phase 2 project comprised the construction of a four-lane structure between Queens and Brooklyn (westbound). It has a 20 ft wide shared-use path that affords pedestrians and cyclists spectacular views of Manhattan. Like its sister structure, it consists of a single-tower, cable-stayed main span and prestressed girder approach spans. Both bridges introduced shoulders where none previously existed and featured lower profiles.
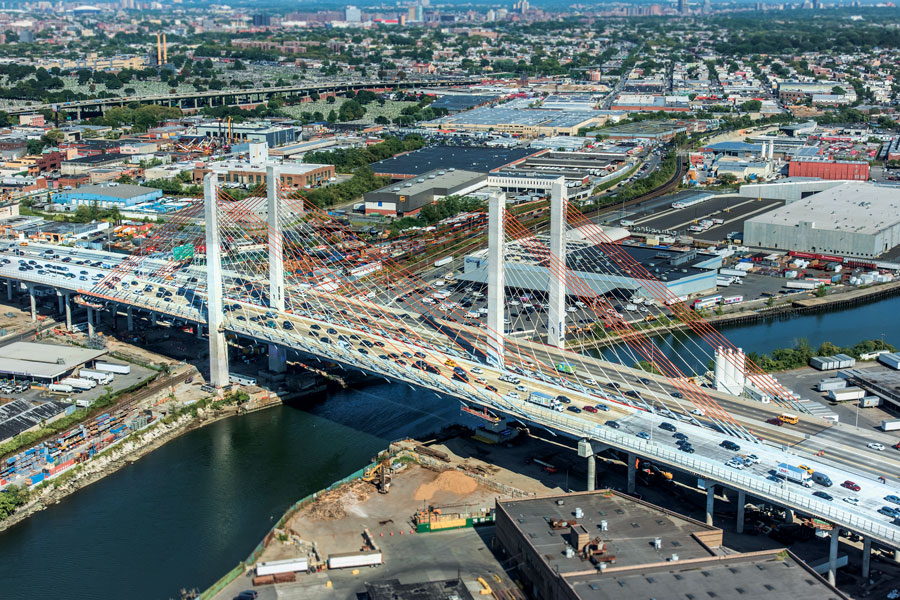
The westbound cable-stayed structure comprises a 609 ft long main span and a 343 ft long back span. Support for the single tower is located on the Queens side of Newtown Creek and extends almost 200 ft above the roadway deck with an above-grade height of 287 ft. This is just below the permitted maximum height, which is in place because of the bridge’s proximity to LaGuardia Airport. The precast concrete deck is supported by steel floor beams and edge girders. The 56 stay cables—placed at various angles to connect the edge girder to the two vertical legs of the pylon tower—comprise nearly 1 million linear ft of steel strands.
Extensive study determined the ideal span lengths and column locations to avoid impacting Newtown Creek, which is a Superfund site; the Class 2, inactive hazardous waste site at the former Phelps Dodge Corp. refining site, which is underneath the bridge in Queens; the Long Island Rail Road tracks; and the local street network below the bridge. The single tower comprises two tapered, reinforced-concrete pylon legs, each supported by four 7 ft diameter drilled shafts that extend approximately180 ft deep and are socketed into rock.
The majority of the upland area bordering Newtown Creek is within one of New York City’s three designated Industrial Business Zones, and the majority of Newtown Creek has also been designated by the city as one of its six Significant Maritime and Industrial Areas. Newtown Creek is currently used for recreational purposes by kayakers, and there is fishing access along its banks.
The structural steel was metalized by applying a coating to it, which improved the steel’s resistance to corrosion and reduced future maintenance requirements—measures to help the bridge achieve a 100-year service life. In addition, a 1 in. thick polyester polymer concrete overlay was applied atop the precast deck panels to protect against chloride infiltration and premature deterioration of the deck. Stainless-steel rebar was used in the deck and the concrete cap beams under the expansion joints to protect against concrete spalling and cracking.
Single-tower, cable-stayed structures like the Kosciuszko Bridge are extremely rare, and the required span arrangement—because of the environmental and local roadway constraints previously mentioned—presented certain design challenges, such as the unbalanced front and back span lengths. As with the eastbound span, a concrete and steel counterweight was added at the end of the back span to account for the large weight differential.
Additionally, on cable-stayed structures, high wind or rain events can cause the cables to vibrate at high amplitudes. Internal hydraulic dampers were installed at each cable to absorb this energy and dampen the vibration effects. This minimizes the motion of the cables, reduces the fatigue effects, and ensures the stability of the structure.
The 16 approach spans employ 79 in. deep, prestressed concrete girders to support cast-in-place concrete decks with span lengths of up to 136 ft. Each pier comprises two 6 ft diameter reinforced-concrete columns with concrete cap beams that are 8 ft deep. The typical foundations use 18 in. diameter concrete-filled, steel pipe piles.
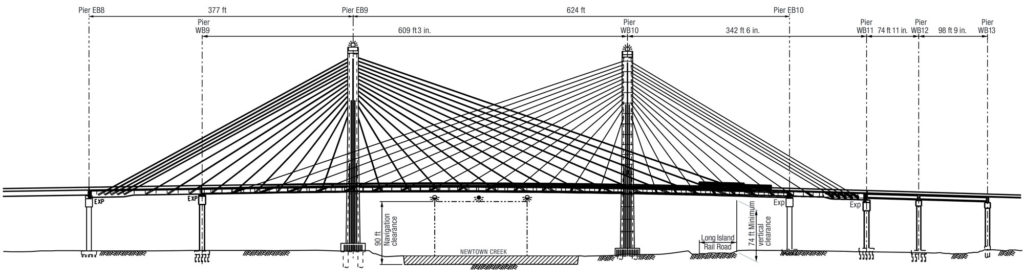
The bridge also includes two simple-span structures in Queens supported on micropiles and integral abutments as well as fill sections retained by precast modular T walls. Lightweight fill was specified in those locations where existing subsurface soil conditions presented risk of settlement. The T walls use a custom form liner to provide improved aesthetics.
The shared-use path fence along the length of the Brooklyn-bound structure is a custom stainless-steel fence that complies with the Americans with Disabilities Act of 1990 and provides a safe, low-maintenance facade. The cable-stayed main span also has a new state-of-the-art aesthetic lighting system, which includes multicolored light-emitting diode (LED) lights that illuminate the cables and tower and can be programmed for dynamic light shows.
In addition to the westbound cable-stayed bridge, phase 2 introduced new open-space plazas and parks to neighborhoods in Brooklyn and Queens. The expanded Sgt. William Dougherty Playground in Brooklyn opened in 2018 and includes children’s play equipment, a water play area with spray showers, a skate park, basketball and handball courts, and a new comfort station.
There will also be a new park in Queens, which is still in the design stage. Construction is expected to begin in 2021. In addition, new open-space plazas in both boroughs that provide passive seating areas to enjoy the views of Newtown Creek and the new structures are scheduled to open this year.
Since 2009, WSP has played multiple key roles throughout the design and construction of the bridge on behalf of NYSDOT. The firm provided design and preliminary engineering services for the overall project (both the east and westbound structures) that included a structural alternative analysis and preliminary engineering, which led to the overall concept for parallel, single-tower, cable-stayed main spans.
The alternative analysis considered numerous structure types for the main span over Newtown Creek, including a box girder, deck arch, and through arch. NYSDOT selected the single-tower, cable-stayed main span concept, which allowed for a single tower on each side of the creek: the phase 1 Queens-bound structure’s pylon located in Brooklyn and the phase 2 westbound structure’s pylon in Queens. This arrangement is not only aesthetically pleasing but also provides a gateway into each community. An added benefit was the ability to increase the span length and therefore avoid impacts to the Superfund and hazardous waste sites.
When NYSDOT decided to proceed with the eastbound bridge as a design-build project, WSP developed the design-build procurement documents and performed the design oversight and quality assurance of the phase 1 contract and an independent analysis of the cable-stayed main span.
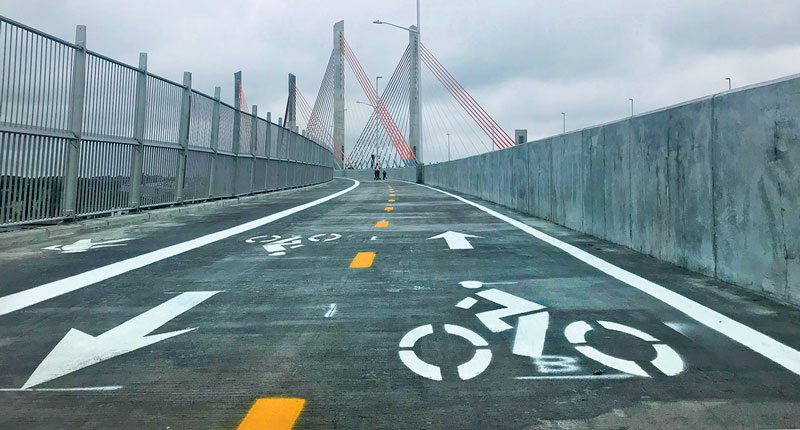
WSP served as lead designer for phase 2 and the engineer of record of the westbound main span and the prestressed girder approach spans. The company also designed the roadway and aesthetic lighting at the main span as well as the new parks and open spaces.
Additional phase 2 consultants included Helen Neuhaus & Associates Inc., the firm that led public outreach efforts, and Hardesty and Hanover, which designed the single-span structures over 54th Road and 54th Avenue at the Queens connector, coordinated the utilities, and designed the bridge’s fire standpipe and drainage systems. Michel Virlogeux, FREng, CorrFRSE, the French structural engineer who designed the Millau Viaduct, one of the tallest bridges in the world, was involved in the early conceptual studies done for the structures’ main spans and helped envision the offset single-tower concept of the parallel bridges.
The design of a complex structure such as this one was exacting and required intricate analysis; however, WSP accelerated the phase 2 design process so that final detailed plans were completed six months ahead of an already compressed schedule. In addition, construction was streamlined to save several additional months in the phase 2 project schedule. Construction of the phase 2 structure was completed within its $318-million budget.
The Kosciuszko Bridge goes the extra mile by delivering a truly signature structure that redefines the spectacular New York City skyline. The replacement bridge represents a big step forward in addressing the growing transportation needs of the region and demonstrates to the nation that it is possible to take on big projects and get them done on budget and ahead of schedule.
—Carol J. Wynperle, P.E.
Ensuring Quality
NYSDOT contracted STV, a firm that specializes in engineering, architecture, planning, and construction-phase services as its construction quality-assurance (QA) engineer for phase 1 to see that the design-build team followed the submitted quality-control (QC) plan. STV had a similar role in phase 2, a traditional design-bid-build best-value project. The firm was the lead partner in a joint venture with the LiRo Group, a construction management firm, which provided resident engineering and inspection services and QA during construction.
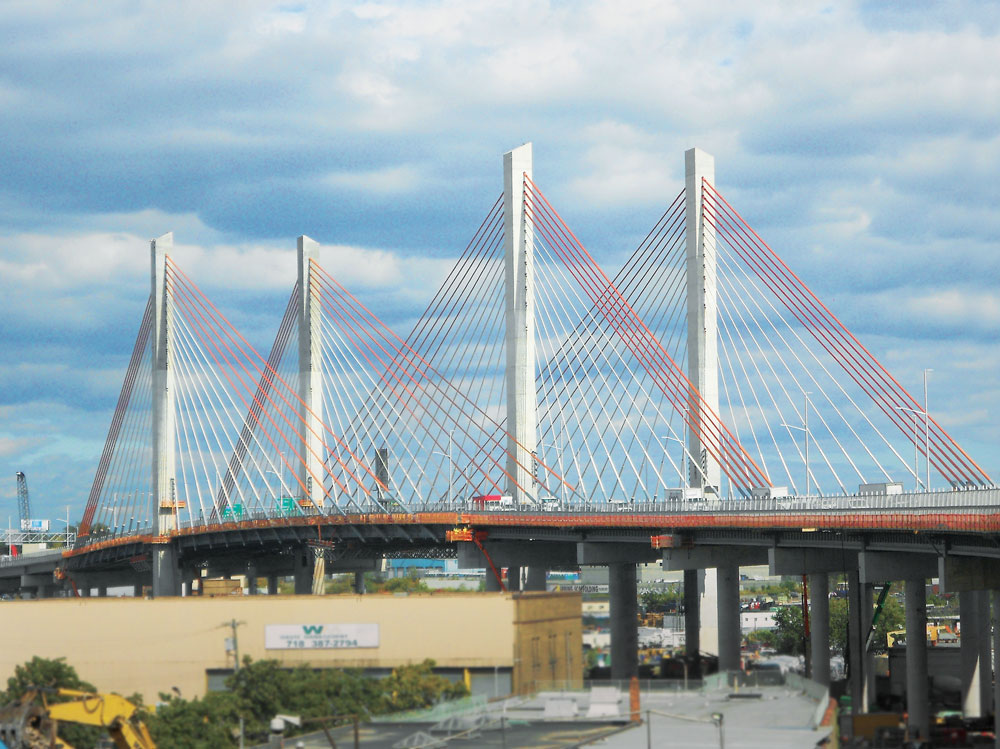
Statistical validation is a new Federal Highway Administration protocol for funding major design-build projects on the national highway system. Phase 1 of the Kosciuszko Bridge replacement program marked the first time it was used for an NYSDOT project. STV was the first firm to perform the testing and statistical verification of QC data using Q-Macros, an Excel-based software package, which was customized to the project criteria and is commonly used for QA in manufacturing processes. Previously, other firms that performed statistical verification in accordance with the federal guidelines used proprietary systems, including all facets of document control and construction administration, requiring substantial resources to implement. STV’s use of an inexpensive and readily available program was a successful, cost-saving solution to the validation task.
Reconstructing this critical bridge in a highly congested area while maintaining traffic flow was a key challenge for the team. In order to maintain the bridge’s existing six lanes of interstate traffic during phase 1, a new eastbound bridge and approaches were constructed adjacent to the existing Brooklyn–Queens Expressway on the south side. This required the acquisition and subsequent demolition of 14 light industrial buildings to create the necessary right-of-way. New connector roadway sections were constructed in Brooklyn and Queens to provide alignment transitions to the existing expressway at each end of the project.
Staged construction allowed the maintenance of traffic on the connectors. Once the new eastbound bridge opened, the original main span and approaches were demolished. The existing main-span through truss was lowered onto a barge for demolition off-site. Removal of the existing approach superstructures was expedited by the use of explosives for controlled felling and demolition at ground level.
Another challenge arose when the construction QA team was called on to support delivery of oversized girders to the urban jobsite. The approach viaducts in Brooklyn and Queens were framed with 8 ft deep, precast-concrete T girders, each up to 80 ft long. Fabricated in Virginia and barged to New Jersey, the girders were loaded onto extended trailers for trucking to the site. Routing for the trucking of the oversized loads was particularly challenging, as the units were more than 100 ft long, requiring very wide turning movements. Backing up was especially difficult, so any blockages along the route had to be avoided.
The construction QA team worked with a special transport unit in the New York Police Department (NYPD) to identify a compatible route and guide the trucks through it. Additional police units were required to maintain an open route on the scheduled delivery nights. This further complicated scheduling because of competing uses of NYPD resources for events in the city. A detailed delivery schedule was drawn up and the design-builder accelerated delivery of some of the units to match available dates for the NYPD.
As the NYSDOT representative on a federally funded project, STV’s team conducted civil rights compliance monitoring and compliance reviews by assessing the contractor’s commitment to equal employment opportunity in all aspects of its employment practices and other obligations related to nondiscrimination, training, and disadvantaged business enterprise contracts.
STV’s solutions supported NYSDOT’s commitment to providing the community with an iconic new bridge designed and constructed for a 100-year life span.
—Thomas Mellett, P.E., M.ASCE, and Robert J. Vaz, CCM
Phase 1 Project Credits (eastbound) Owner New York State Department of Transportation (NYSDOT) General contractor Skanska USA–Kiewit Corp.–ECCO III Enterprises Inc. (SKE), New York City Designer/chief bridge engineer HNTB, New York City Quality assurance design WSP USA, New York City Quality assurance inspection STV, New York City Foundation engineer of record Matthew Riegel, P.E., D.GE, M.ASCE, HNTB
Phase 2 Project Credits (west- bound) Owner NYSDOT General contractor Granite Construction Northeast Inc., Watsonville, California Erection engineer (cable-stayed span) COWI North America, New York City Designer WSP USA Resident engineering/inspection STV–LiRo Group joint venture, New York City Survey and right-of-way mapping MJ Engineering, Gahanna, Ohio Wind engineering RWDI, Guelph, Ontario, Canada
This article first appeared in the September 2020 issue of Civil Engineering.