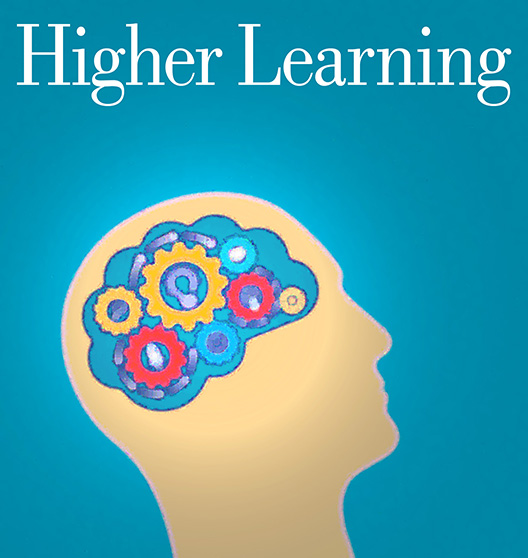
A team of researchers at the University of Kentucky (UK) in Lexington are creating, testing, and deploying a family of lightweight, carbon fiber-reinforced polymer (CFRP) composite products, dubbed CatStrong, that are being developed to repair damaged and deteriorating bridges in the state. What’s more, they are also being used in undergraduate civil engineering curriculum for teaching purposes to demonstrate composite strength.
Issam Harik, Ph.D., M.ASCE, and Abheetha Peiris, Ph.D., P.E., M.ASCE, lead the research team. Harik is the director of UK’s structures lab, where the research and testing for the CatStrong products are performed, and Peiris is a research engineer for the university’s Kentucky Transportation Center and an adjunct assistant professor in the Department of Civil Engineering. Rounding out the team are undergraduate, graduate, and postdoctoral students, who are instrumental in the products’ research. “The students assist in every aspect of the CatStrong development. They prepare large and small samples and collect and reduce data” and perform other tasks in the structures lab, Harik said in written answers to questions posed by Civil Engineering. “A number of graduate students’ M.S. and Ph.D. theses are based on the testing of the products.”
CatStrong, according to Harik, is a portmanteau of the school’s mascot—the Wildcats—and the word “strong.” The suite of products includes CFRP rod panels, wraps, and fabrics that are primarily used for bridge repair. “To date, we have repaired almost forty bridges [in Kentucky], and the majority use the CatStrong products. All proceeds go to support students and product development,” Harik said.
Once the product is applied to a structure and cured, the result is a concrete pier, pile, beam, or span that is stronger than the as-built (or original) structural element. Using CFRP products in bridge repair is a cost-effective, quick solution to traditional repairs, and the bridge can remain in use during installation in most cases.
“To date, we have repaired almost forty bridges [in Kentucky], and the majority use the CatStrong products. All proceeds go to support students and product development.” — Issam Harik, Ph.D., M.ASCE
Harik has spent more than a decade developing the CatStrong materials, with research and testing beginning in 2008. Two years later, after continued testing, trials, and modifications, the first product, the CatStrong rod panel, was developed. A year later the first field application of the panels was performed, with testing continuing until 2017. “In May, we received a patent for the rod panels,” Harik said. “The names of three students who assisted us during the development stage are included on the patent inventor list, along with Dr. Peiris and me.”
Harik and Peiris work directly with stakeholders in the products’ deployment. “When a repair project is identified, Dr. Peiris and I communicate and meet on a regular basis with representatives from the Kentucky Transportation Cabinet and the district engineers [in which] the bridge is located,” Harik said. “We also supervise the repair and submit a final report to the district and cabinet that includes the design and construction process that was carried out along with the bridge load rating before and after the repair.”
Because of the COVID-19 restrictions in place, work in the structures lab and in the field has been suspended. Harik hopes the team will be able to resume product testing and bridge repair in the fall.
WHILE THE CATSTRONG products feature heavily in the team’s work in the structures lab, they also play a role in civil engineering undergraduate curriculum. Peiris—along with Clark Graves, Ph.D., P.E., P.G., an adjunct assistant professor in UK’s Kentucky Transportation Center, and Kamyar C. Mahboub, Ph.D., P.E., F.ASCE, the Lawson professor of civil engineering at UK—teaches CE 381 Civil Engineering Materials I. The class and lab introduce students to the properties of civil engineering construction materials, including CFRP composites.
“While most of the sections covered in the class and the teaching methods are probably common with many undergraduate engineering institutes around the country, one aspect that may be unique is the section on composites,” Peiris stated in written statements to Civil Engineering. “As FRP materials are being utilized more in both new construction and especially in rehabilitation and retrofit of existing bridges and buildings, it was decided to include a section on composites within the CE 381 curriculum.”
In addition to the composites lectures, the teaching team decided two years ago to augment the in-class component to include two lab sessions. The overall lab schedule is comprehensive, with labs not only in composites but also steel, aggregate testing and gradation, concrete testing and mixing, and asphalt mix design. There is also time built into the lab schedule for group presentations.
In the concrete labs, students are tasked with making three concrete cylinders according to set design specifications. One extra concrete cylinder is cast and set aside to be used during the upcoming composites portion of the lab. Several weeks after the cylinders are made, two are tested in compression and one in splitting tension, according to Peiris. All work is done in groups, and each is assigned a design strength for its concrete cylinders. “The final test results are shared among groups, and the students evaluate any correlation found between strength and respective mixes.”
“The students readily understand the benefits of composite material when they see the degree of strengthening achieved by the FRP-wrapped cylinder beyond what they tested previously.” — Abheetha Peiris, Ph.D., P.E., M.ASCE
FRP fabrics, according to Peiris, are commonly used to “confine concrete columns and improve their load-carrying capacity.” The students get to test this with their concrete cylinders during the composites section. The extra cylinder that was made during the concrete lab and the cracked cylinder (which was split in two) are wrapped in CFRP materials not long after the groups have completed the compression and splitting tension tests.
The next step is to test the wrapped cylinders in compression, which is usually done a week after they have been wrapped. Peiris provides the material properties of the CFRP, and using American Concrete Institute guidelines, the students must determine the increased load-bearing capacity compared with the cylinders’ unwrapped capacity. “The students readily understand the benefits of composite material when they see the degree of strengthening achieved by the FRP-wrapped cylinder beyond what they tested previously,” Peiris noted. But that is not the only phenomenon they observe. “The more surprising test for the students is usually the cylinder that was put back together and wrapped following the splitting tensile test. Especially for lower-grade concrete, the CatStrong carbon fabric used provides sufficient confinement to increase the cracked cylinder strength above the original concrete strength.”
Peiris explained that after a field repair project, leftover CatStrong CFRPs are stored in the lab, and that is what they use in place of purchasing other brands of FRP materials. Besides the CatStrong wraps, students have the opportunity to “handle” FRP rebar, fabrics, pultruded laminates, and pultruded sections, Peiris said. “While it is easy to have a student feel the weight difference between the same size steel and carbon FRP rebar and let them know that the carbon FRP, while being less than a quarter of the weight, is more than four times as strong, it is much more convincing to show the students the material being utilized and tested in a way that it is actually used in real-world applications.”
Unfortunately, testing the strength of the CFRP materials for themselves was not an option in the spring when in-person classes were canceled and learning moved online. Instead, Peiris and the other instructors recorded themselves performing the lab exercises, and students watched and then reported on the data they gathered.
If in-person instruction resumes this fall, the lectures will be given twice, splitting the cohort in two so that social distancing can be maintained. However, that will not be the case for the labs. “They will either be presented via video or have one person carry out activities, while group members observe and take notes, maintaining social distance,” he stated. It is not the best solution, but he recognizes that this is how learning must be conducted. He is concerned, however, by what they will not be able to do: build their teamwork skills. “One of the biggest components of lab work is working in a group, which the students miss out on when the labs are virtual,” Peiris said.
Not only will they miss out on group activities, but with virtual labs they will lose the opportunity to appreciate the beauty and properties of the various materials they will learn about in the lectures, according to Peiris. “It’s difficult to show on a video how light a composite rebar is when compared to a steel rebar or to feel how warm a steel rebar gets when tested in tension or how bad a concrete cylinder would turn out if you don’t follow American Society for Testing and Materials standards!”
This column first appeared in the September 2020 issue of Civil Engineering.