The organization behind New York City’s Tammany Hall was once infamous for political corruption. But the former Tammany headquarters building has been reborn as modern, mixed-use commercial space. Although two historically recognized facades were preserved, the rest of the original structure was replaced, expanded vertically, and reimagined with a glazed grid shell dome crowning the project.
Tammany Hall was once notorious for political patronage and corruption, symbolized in editorial cartoons by a sometimes rapacious, sometimes pathetic tiger. But the Tammany Society, the political organization that built the hall in the late 1920s on the northeastern corner of New York City’s Union Square, was actually named more than a century earlier after someone with a far better reputation: the Native American chief Tamanend, a leader of the Lenape people who once lived in the New York area.
The Lenape’s creation story features a turtle rising from the sea, and it was this turtle that inspired a recent reimagining of the Tammany Hall building, an effort that preserved two of the historical brick facades but essentially gutted the interior. Most of the old building — a three-story, neo-Georgian-style steel-framed structure — was then replaced with a new six-story concrete structure crowned by a glass-and-steel grid shell dome designed to resemble a turtle’s shell.
Now known as 44 Union Square, the project added approximately 30,000 sq ft of useable space to the building and features a total of 72,000 sq ft of commercial and retail space.
New York City-based BKSK Architects, which won an invited competition for the project, led the renovation. International engineering firms Thornton Tomasetti and Buro Happold served as the project’s structural engineer and facade engineer, respectively. Although the major structural work was completed last year, the final build-out of the interior spaces awaits a tenant. The building is owned by Reading International Inc., of Culver City, California, and the project was overseen by the owner’s representative, Edifice Real Estate Partners, of New York City. The construction manager was CNY Group, also based in New York City.
Preserving a landmark
Over its useful life, Tammany Hall featured numerous owners, tenants, and programs. The Tammany Society sold it to the International Ladies Garment Workers Union in the 1940s. By the 1980s, the building, which featured a large auditorium, was being used as an off-Broadway theater. It also housed a film and acting school in the 1990s before being sold to the current owners in the early 2000s. As a result of the building changing hands so often, the interior had been altered considerably, “cut up … into a series of half levels and a warren of spaces,” notes Todd Poisson, AIA, a partner at BKSK Architects.
The site was designated a landmark building in 2013 by the New York City Landmarks Preservation Commission. So much else about the structure had changed over time, however, that the landmark designation pertained primarily to the northern and western facades, which featured brick and limestone construction with numerous ornamental details. The northern facade, facing East 17th Street, has an arched pediment and a medallion of Chief Tamanend, while the western facade faces Union Square East and features a classical portico with columns and a triangular pediment.
By 2014, the owners proposed converting the site into a modern mixed-use building while preserving the two historical street-front facades and adding the dome as well as a balcony to the roof. Although the landmarks commission rejected that initial design, a new proposal submitted in 2015 won unanimous approval by the commission. The new design replaced the balcony with a reimagined version of the building’s original hipped roof and changed the geometry of the dome “to have a more classical proportion when viewed from the square,” among other alterations, says Poisson.
The eastern and southern facades were not preserved, because they were located adjacent to the walls of other buildings and had not been given landmark status, notes Marco Coco, P.E., S.E., a New York City-based vice president of Thornton Tomasetti. It would also have been more difficult and expensive to brace those walls during the demolition of the interior.
“We did try to salvage as much of the existing brick as possible and reuse it on the new walls that were built at those locations,” adds John Ivanoff, an associate principal in Buro Happold’s New York City office.
The northern and western facades featured three- and four-wythe deep brickwork and limestone lintels, which were supported during the demolition and construction phases by steel bracing towers designed by the shoring engineer, Howard Shapiro & Associates. The bracing system included steel walers on the exterior and interior of the walls to sandwich the existing facade, says Coco. These horizontal members were supported by the main exterior bracing towers, which were located on the sidewalks surrounding the Tammany Hall site. The towers were not removed until the new interior concrete structure was in place and the original facade walls had been secured to it by a series of steel clip angles and epoxy anchors, Coco notes.
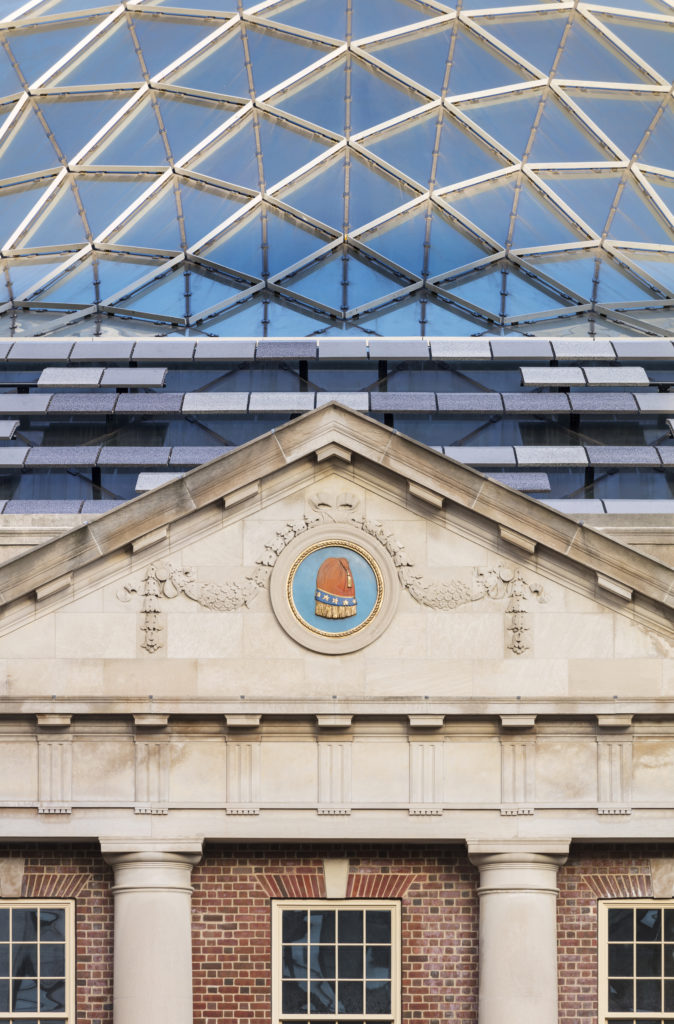
The original brickwork was monitored for vibration and potential cracking throughout the project. Although some cracking and settling did occur, it was minor, Ivanoff notes. A series of rooftop parapets turned out to be in worse condition than expected and had to be replaced rather than repaired. The new parapets feature sections of both salvaged and new bricks, new balustrades installed with spring-loaded dowels, and new reinforced-concrete masonry units that replaced the original brickwork in some locations.
In addition to demolishing the original interior, the project team also excavated the western side of the site to match the existing basement level on the eastern side, which was about 5 ft deeper, says Poisson. The new interior of the building is founded on new spread footings bearing on rock. The existing foundation wall and footings around the perimeter of the building were retained, “mostly because the existing steel framing was integral with the landmarked facade,” says Coco. “The existing perimeter column spread footings were enlarged to support new loading conditions.”
Because the rock profile at the site slopes from approximately 17 ft below street level along the western side to more than 25 ft below grade on the eastern edge, some of the new footings on the eastern side were changed to micropiles. This was done “so we didn’t have to keep digging and potentially undermine the neighboring buildings,” Coco explains. The project team monitored the adjacent buildings during the construction of the new foundations.
The building’s new interior framing system features reinforced-concrete shear walls, typically 12 in. thick, to resist lateral forces and reinforced-concrete floor slabs typically 11 in. thick. Existing steel columns embedded within the historical facade walls were also encased in concrete to form piers that provide vertical and lateral support and help preserve the integrity of the historical facades, Coco says. The concrete for these piers was placed monolithically with the new slabs, and the piers themselves are supported on new concrete footings that tie into the facade columns’ original footings.
Topping it off
To design the new dome and its support structure, Thornton Tomasetti worked closely with the fabricator and erector, Josef Gartner GmbH, a division of Permasteelisa, from Gundelfingen, Germany. The glazed structure spans 150 ft in a roughly northwest to southeast direction and 75 ft in the northeast to southwest direction. It features a steel tube framing that was welded together at intersecting nodes in the lower portions of the dome and bolted together at the higher portions to accommodate the dome’s geometry. The main steelwork features rectangular steel tubes that measure approximately 6 by 3 in. in cross section. These support more than 800 triangular glass panels that form a surface area of approximately 12,000 sq ft.
The edge of the dome undulates slightly on the northern and southern sides of the structure, rising like the openings in a turtle shell — especially where it seems to “peak up over the arched pediment on the 17th Street side,” notes Poisson.
Although most of the new floors within the building feature floor-to-ceiling heights of roughly 12 ft, the dome levels feature heights of 19 ft. The uppermost level, the sixth floor, also resembles an elevated platform at one end, standing on pillars to provide a balconylike space within the dome.
To support the dome, the design team used a reinforced-concrete retaining wall system at the new fourth-floor level, a combination of horizontal restraining and sliding bearings, and a curved reinforced-concrete corbel structure that surrounds the new concrete core, Coco explains.
A thickened floor slab — roughly 16 in. deep — along the northern and western facades and part of the southern facade supports the new retaining wall structure. The concrete wall is designed to support the vertical and lateral loads from the new dome, including the thrust forces imposed by the dome’s free-form geometry.
The final design of the dome steelwork became quite complex in certain locations, especially at critical nodes where multiple steel members came together. In particular, some of the nodal supports were changed from laterally restrained to roller supported in order to reduce the horizontal demand on the supporting structure, says Coco. This was especially necessary where the elevator core walls support the corbel structure.
The original Tammany Hall building had appeared to be topped by a hipped roof made from slate, but this was largely just an aesthetic feature — a false top that concealed a flat roof underneath. To mimic the historical appearance of the original building, however, the design team developed a series of terra-cotta sunshades that were installed along the western facade and a portion of the northern facade. Measuring roughly 1 ft tall and varying from about 18 to 24 in. long, the fixed sunshades are supported on a steel subframe that connects back to the dome’s steel structure. Located above the glazing for the new fourth-floor offices, the sunshades will provide thermal comfort and glare protection.
The dome’s glass is tinted rather than fritted because the proximity of the workspaces to the glazed surface meant that the harsh sunlight would actually be visible between the frits — an effect that the architects learned by studying other glazed domes around the world.
Fitting in
Because of Tammany Hall’s proximity to other buildings and the general traffic congestion of downtown New York City, there was almost no space available for the teams to assemble components on-site, Ivanoff notes. Fortunately, the project relied mostly on prefabricated elements that were assembled off-site and then “fit together like a kit of parts and not stick built,” he explains. This was especially true for the steel elements that were put together in Germany and shipped to the United States in large components that fit inside cargo containers. The glass panels often arrived on the same day they were being installed, minimizing storage requirements.
During the erection of the dome, large steel pieces were assembled in a stepped or ladderlike formation, and strategic locations throughout the dome had to be self-supporting prior to being enclosed. As the steel erection team moved ahead, a second team came behind it, installing the gaskets and glazing. These teams were “literally climbing over this organic shape,” which is not flat anywhere or easy to walk on, Ivanoff adds.
But thanks to these efforts and the work of all the members of the design and construction teams, the former Tammany Hall has been preserved and improved. Its two historical facades still form part of the shell that surrounds the building, while a modern shell now crowns the structure — rising, like the Lenape people’s legendary turtle, toward a new and promising future.
PROJECT CREDITS
Owner: Reading International Inc., Culver City, California
Owner’s Representative: Edifice Real Estate Partners, New York City
Architect: BKSK Architects, New York City STRUCTURAL ENGINEER: Thornton Tomasetti, New York City office
Facade Engineer: Buro Happold, New York City office
Dome steel fabricator and erector: Josef Gartner GmbH, a division of Permasteelisa, Gundelfingen, Germany
Geotechnical engineer: RA Engineering LLP, New York City
Mechanical, electrical, and plumbing engineer: Dagher Engineering, New York City
Construction manager: CNY Group, New York City
Historic preservation consultant: Higgins Quasebarth & Partners, New York City
SIDEBAR
Rebranding Tammany
By Robert L. Reid
Unlike the infamous political organization behind New York City’s Tammany Hall, the group’s namesake — Chief Tamanend — was considered a legendary leader of the Lenape people, notes Todd Poisson, AIA, a partner in the architecture firm BKSK Architects that helped convert Tammany Hall into the modern 44 Union Square mixed-use project. Famed for signing a peaceful coexistence treaty with William Penn in the 1680s, Tamanend also had a reputation of being “someone who’d listen to all voices,” Poisson explains.
Although the design brief for the project competition implied that the owners felt “it was time to move away from the name Tammany,” Poisson says, BKSK’s research into the history of Chief Tamanend and the Lenape people offered “an opportunity to rebrand ‘Tammany’ in a perhaps unexpected way.”
In the Lenape’s creation story, “a giant turtle rose from the seas to create the land,” Poisson explains. That imagery, together with the goal of enlarging the property vertically to create additional space, led to the idea of the shell-like dome. The best design to accomplish that vision involved a free-form grid shell — a structural system that is highly flexible, requires no internal supports, and can be optimized through parametric software “in a way that would be expressive of an organic shape, such as a turtle shell,” Poisson says. At the same time, the dome would appear classically proportioned for its Union Square setting.
Fortuitously, the design team discovered examples of other neo-Georgian-style buildings that were topped by domes, including some that had their domes added long after the original buildings had been constructed. Although such discoveries were helpful in convincing New York City’s Landmarks Preservation Commission to approve the dome scheme, the design team also sought the approval of another critical stakeholder: the Lenape people themselves.
“It was very important to us to be sure we weren’t appropriating cultural imagery inappropriately,” Poisson explains. So, he contacted New York City’s Lenape Center to discuss the project. The Lenape leadership not only approved the project, but two of the organization’s cofounders — Hadrien Coumans and Joe Baker — also came to the newly completed building in October 2020 to perform a traditional blessing ceremony. Designed to acknowledge the past, present, and future inhabitants of the site, the ceremony began outside the building with a prayer of well-being and an honor song and concluded within the new dome.
“We thank the Lenape Center for their guidance and support of the use of Lenape imagery of a rising turtle to inspire Tammany Hall’s new crowning dome,” Poisson said at the event. “We hope Tammany’s new glass dome appears forever frozen at the very moment that the turtle is breaking through the surface of the sea, shedding water from its shell. Because it is at this moment that anything is possible.”
This article first appeared in the May/June 2021 issue of Civil Engineering as “Tammany Rising.”
Interesting renovation.
valued structure.
Soussan Bathaee
SCIENTIST