The distinctive curved geometry of the Louis Armstrong New Orleans International Airport terminal was designed to withstand harsh weather while concurrently improving the overall passenger experience. The design and construction team’s ingenuity kept the project to its fast-paced schedule even with major changes to the scope of the program.
The new state-of-the-art Louis Armstrong New Orleans International Airport terminal opened in November 2019, making it the first major replacement airport terminal to open in the United States in the previous 10 years. The signature design and fast-paced schedule of the new terminal required ingenuity from its design and construction team.
The three-level, three-concourse, 35-gate, crescent-inspired terminal was a massive undertaking. It featured modern amenities designed to meet future passenger needs, updated security systems, and aviation industry best practices and operations. Often identified by its three-letter airport code MSY, the terminal provides world-class concessions that highlight the flavor of New Orleans’ distinct culture. The building’s unique crescent shape, as well as a late-stage addition to the building program, presented a series of intricate design, engineering, and construction challenges.
The design of this innovative $1 billion terminal began in 2011 — eight years before it would officially open — thanks in part to efforts by then-New Orleans Mayor Mitchell J. Landrieu, who pressed the New Orleans Aviation Board to commission an analysis for a new international terminal to replace the existing one, which dated to the 1950s. In 2013, airport officials decided to move forward with a long-term strategic development plan to build the new terminal on the north side of the airfield where it could tie into the existing runways. In 2016, construction commenced on the new terminal, which initially was planned as a 30-gate, 650,000 sq ft facility with two concourses.
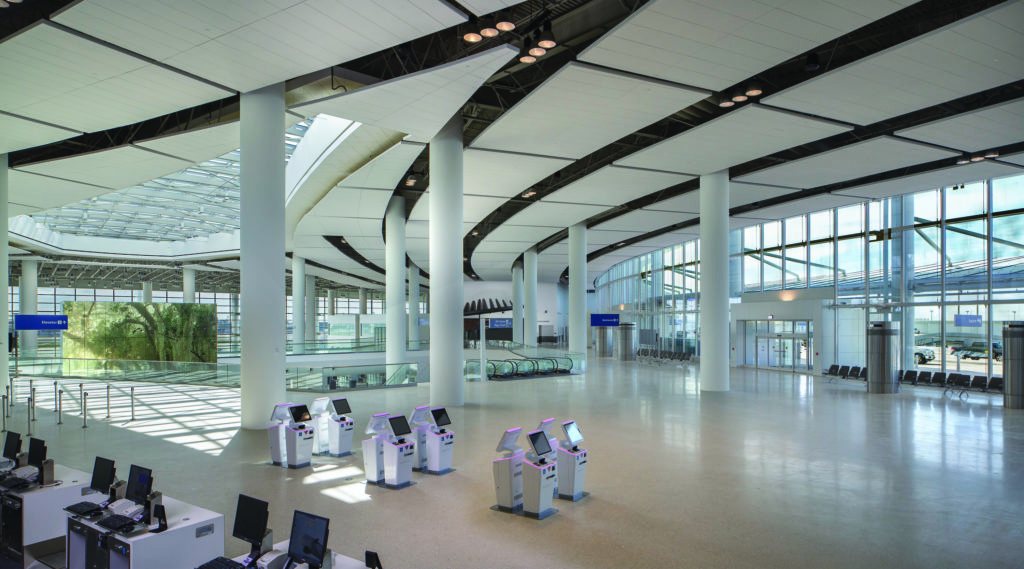
Funding for the MSY project was provided by grants from the Federal Aviation Administration, Airport Improvement Program, Transportation Security Administration, Louisiana State Aviation Trust Fund, passenger facility charge collections, general airport revenue bonds, and other sources. This funding, which amounted to nearly $900 million, covered the initial scope, which included the terminal building and two new concourses, designated Concourse B and Concourse C. Public bonds provided additional funding for changes that were made during construction, including the addition of a third concourse, designated Concourse A.
The terminal’s design, based on an initial concept by Pelli Clarke Pelli, was developed and completed by the Crescent City Aviation Team, a joint venture between Atkins North America, eStudio Architecture, and Leo A Daly. The aviation team also included Walter P Moore for structural engineering.
A defining aspect of the new terminal is the unique geometric design. From an overhead view, the terminal building appears as an inverted “T” with curved sides resulting in a crescent-shaped structure that features constantly curving and flowing walls. The geometry is based on multiple radial grid systems founded on three primary work points that drove the shape of not only the structural grid but also the facade. The building’s curved form pays tribute to the city that the airport serves — a nod to both New Orleans’ nickname, The Crescent City, and the area’s landscape, which was carved out by the Mississippi River. The west side of the terminal ties into an elevated departures roadway that serves the ticketing hall at the upper level, and the east side handles the arrivals roadway that ties into the baggage claim at the lower level.
The shape of the terminal building roof was designed as if it had been sculpted out of a sphere with an approximately 5,000 ft radius. This unique attribute allows rain to flow naturally to a perimeter drainage system from the central focal point of the terminal, which consists of a large skylight above an open atrium. From an architectural standpoint, Pelli Clarke Pelli wanted the building to be aesthetically pleasing while also preserving the unique architectural experience for arriving passengers. By minimizing the rooftop equipment, the design preserves the unique shape of the terminal roof and provides ample daylight for the atrium and the “jazz garden” located below at the arrival level.
During the design phase, the spherical roof and the radial grids were parametrically controlled and carefully considered to arrive at the final desired shape and layout of the terminal. The use of the Rhino 3D modeling platform and associated Grasshopper visual programming plug-in — both developed by Robert McNeel & Associates, of Seattle — enabled the Walter P Moore team to examine various options simultaneously to ensure synergy between the architectural intent and the structural design.
One of the greatest design challenges was realizing the architect’s vision of sweeping open spaces within the geometry of the structure while staying within the budget. As a result, multiple rounds of value engineering led to numerous design changes throughout the project. The parametric model was an invaluable tool in avoiding delays. For example, the roof geometry of the terminal building and the transition to the roof of the concourses were parametrically modeled and adjusted as the architect developed the preferred form.
For the interior of the main terminal building, the innovative floor plan resulted in a highly improved passenger experience from the former facility. The inverted T-shaped floor plan enables passengers to navigate the airport with intuitive wayfinding. For example, the departures-level atrium looks down onto the unified security checkpoint and offers a view of the entire length of concourses B and C. There is also a large three-story central atrium that welcomes arriving and departing passengers into a soothing environment bathed in natural light.
Operational improvements include a single consolidated security checkpoint that provides an open, column-free space for as many as 17 security lanes, and an interstitial, in-line baggage system that allows passengers to drop off checked baggage at the ticket counters. An extensive concessions program also provides more than 40 unique restaurants and shops.
After the initial designs were approved and construction had begun with groundbreaking and pile driving for the new terminal, the project soon ran into a sizable hurdle when the City of New Orleans realized in 2017 that passenger growth at the airport was increasing at a faster rate than anticipated. To meet this unexpected growth, the city decided to expand the original program. By accelerating the design and construction of a third concourse — Concourse A — the planned 30 gates were increased to 35 and the overall size of the terminal was increased from 650,000 sq ft to 972,000 sq ft.
When this design change was implemented, 30 percent of the foundations were already in place and the structural steel was being fabricated and erected for the portion of the terminal at which the added concourse would be connected. Walter P Moore was tasked with designing the new third concourse, which was designated as the international concourse and thus required a dedicated baggage system. Under the original plans, only a single gate in Concourse B had been intended for international flights.
To meet the challenges of the third concourse, Walter P Moore’s team leveraged a digital platform that combined several design software systems to manipulate the integrated structural and enclosure model simultaneously. These tools included Grasshopper; Revit, developed by Autodesk Inc., of San Rafael, California; and Dynamo, developed by Dynamo Software Inc., of Watertown, Massachusetts. As a result, the team was able to rapidly redesign the primary structure and enclosure systems in several days as opposed to several weeks, helping keep the project on track and on budget.
The design of Concourse A was expedited and completed while the engineers were simultaneously providing construction administration services for the main terminal as well as Concourses B and C — all without interrupting the overall schedule. Walter P Moore managed the added scope while collaborating with the architect to facilitate a seamless transition, both visually and functionally, from the terminal building to the new third concourse. The use of building information and parametric models helped provide quick and accurate coordination with other firms on the project, especially those involved in the mechanical systems. Thanks to such tools and collaboration, Concourse A was completed concurrently with the remainder of the originally planned work.
The new terminal building measures approximately 1,500 ft wide in the east-west direction and 700 ft long in the north-south direction, and each of the concourses measures approximately 600 ft long in the north-south direction. Columns in the terminal consist of 40 and 48 in. diameter circular concrete elements. Similarly, the concourse columns are 28 and 30 in. in diameter. The typical column grid spacing in both the terminal and the concourses is 45 ft.
Because of the radial grids and the terminal’s geometry, circular columns were chosen to effectively connect the framing and enhance constructability. Several options were initially considered, including concrete-encased wide-flanged columns, concrete-filled pipe columns, and reinforced-concrete columns with steel pipe sleeves at the connection nodes. Ultimately, the design team selected the reinforced-concrete column with connection nodes as the most economical option. A high-strength, flowable, self-consolidating concrete mix was then used for the column concrete to minimize honeycombing and concrete defects.
The primary gravity load carrying system consists of composite steel floor framing and a deck supported by reinforced concrete and steel columns. The roof gravity system consists of a roof deck on steel joists and beams along with steel vierendeel trusses at select locations to aid in mechanical coordination. At the roof connection nodes, steel wide-flange stub columns were deployed to improve the field fit-up between the roof framing and the circular concrete columns below. The lateral load system consists of a hybrid steel-and-concrete moment frame system along with select braced frames to help support some of the lower levels.
Because of poor soil conditions at the site, the substructure design — including the foundations and the structured slab at grade — was a critical aspect of the terminal’s design and construction. The foundations feature driven precast concrete piles 110 ft long and 14 in. square. Pile caps support the columns, and the at-grade slab — supported by intermediate slab piles — was structured to span between the piles, grade beams, and pile caps.
The region’s weather also presented challenges for the design and construction teams. In 2005, Kenner, Louisiana — home to MSY airport — was one of the areas hit hardest by Hurricane Katrina. The storm damaged an estimated 2,800 homes in Kenner and caused millions of dollars in damage, according to a press release from the city. As a part of Kenner’s post-Katrina recovery plans, the airport was required to have a facility that could withstand 150 mph winds, in accordance with ASCE/SEI 7-10 Minimum Design Loads for Buildings and Other Structures.
Although designing a large structure to withstand hurricane winds can be quite challenging, the geometry of the terminal — especially the spherical roof and curved curtain wall — enhanced the building’s aerodynamic performance under wind loads. To take advantage of the building’s shape and ascertain the wind loads accurately, Walter P Moore engaged BMT Fluid Mechanics as a wind-tunnel consultant. BMT created a scale model of the proposed airport structures and their surroundings along with a site-specific climatological study to derive the primary wind directions for use in the wind tunnel.
The model featured hundreds of wind-pressure sensors/monitors that were subjected to hurricanelike conditions to help identify more accurate wind pressures compared with code-level wind-pressure calculations. In some instances, the geometry of the building resulted in wind pressures higher than the code would prescribe. The testing process also determined wind behavior and pressures based on project-specific geometry and context. BMT provided the test results in the form of Excel spreadsheets and corresponding colorized Rhino surface models. The resultant wind pressures were then digitally mapped to Walter P Moore’s models to engineer the enclosure and structural systems of the building. The Rhino model isometric views were also used to document the wind loads for the project on the design drawings.
The analysis of the wind tunnel model’s results and subsequent engineering ensured that the terminal’s structure, cladding, and glazing systems would provide a high level of hurricane resistance should such an event occur. Walter P Moore’s enclosure team performed a variety of digital simulations in coordination with the architectural, structural, and mechanical teams. The analysis included daylighting, shading, reflectivity, glare, and solar concentration. These studies allowed the team to mitigate risks from environmental factors while simultaneously optimizing such design elements as the overhang lengths, sunshade locations and depths, glazing coatings, and ceramic frits.
Additionally, the terminal’s glass curtain wall was designed to accommodate ample natural light while also providing open views of the airfield. For example, the terminal’s south wall measures nearly 800 ft long with a 50 ft high glass curtain wall. To ensure open views, a lightweight secondary steel truss and cable support system was incorporated into the curtain wall design. Sunshades allow daylight to enter the space year-round while blocking direct sun during hot summer months.
If preparing for a hurricane was not challenging enough, the design also had to address seismic issues. Although New Orleans is not generally associated with seismic hazards, the very poor soils at the MSY site, coupled with thermal considerations because of the facility’s immense size, meant that the new terminal had to be able to withstand substantial seismic loads. The design earthquake forces were equivalent to 0.07 g, which falls into the International Building Code’s Seismic Design Category B. Consequently, expansion joints were used to subdivide the terminal into 10 distinct “buildings” — an approach that will allow the overall structure to “breathe” and relieve stresses under cyclical seasonal temperature shifts and be apportioned to withstand the design-level earthquake. It proved especially challenging to coordinate the multiple expansion joints and slide bearing connections required to enable seismic movements between the various subdivisions of the terminal. These special elements affected every building system well beyond the structure. For example, any mechanical ducts or radiant tubing that crossed an expansion joint needed to be detailed to allow building expansion and contraction.
Aesthetically, these joints and connections had to blend in with the facade and be concealed to preserve the design intent. Mechanically, in addition to all the pipes, ducts, and conduits that crossed these joints, the baggage-handling conveyors, catwalks, and other systems also needed to accommodate the anticipated movements.
The use of Revit and Autodesk’s Navisworks software for documentation and coordination — in concert with Rhino design software and the Grasshopper plug-in — was critical throughout the design and construction processes. Revit and Navisworks offered a single platform through which the entire building team could communicate any changes and solve any issues related to the project. Rhino and Grasshopper were also used to define and manipulate geometry and at times to verify the design against the construction models. From a design standpoint, the utilization of such parametric tools and digital workflows was critical for flexibility and timeliness as well as for detailing and planning the construction tolerances.
Since opening in November 2019, the new Louis Armstrong International Terminal has received acclaim from the aviation community and passengers alike and now serves 16 commercial airlines. The project is a major economic driver and focal point for New Orleans as well as one of the airport industry’s most transformative terminals in the last decade.
PROJECT CREDITS Client New Orleans Aviation Board Design architect Pelli Clarke Pelli, New Haven, Connecticut Architect Crescent City Aviation Team joint venture (Atkins North America, Tampa, Florida; eStudio Architecture, Houston; and Leo A Daly, Washington, D.C.) Structural engineer Walter P. Moore and Associates Inc., various offices; and Julien Engineering and Consulting Inc., New Orleans Civil engineer Atkins, part of SNC-Lavalin Group, Montreal General contractor Hunt-Gibbs-Boh-Metro joint venture, New Orleans Program manager WSP, Montreal Steel fabricator Hirschfeld Steel, San Angelo, Texas Mechanical, electrical, and plumbing and telecommunications engineers Syska Hennessy Group, New York City; Lucien T. Vivien Jr. & Associates Inc., Metairie, Louisiana; Marrero, Couvillon & Associates, Baton Rouge, Louisiana; and Burns Engineering, Philadelphia Baggage systems engineer BNP Associates Inc., Denver Wind tunnel consultant BMT Fluid Mechanics, Teddington, England, United Kingdom
This article first appeared in the January/February 2021 issue of Civil Engineering as “Terminal Velocity.”