A SMALL, IRREGULARLY SHAPED, and sloping site in Portland, Oregon, that was considered practically worthless now hosts a five-story mixed-use building constructed through an innovative use of mass timber elements. Originally known as B76, according to the city’s designation of lots, the new building has been named Sideyard and is expected to eventually house offices along with retail and restaurant spaces. Although structurally complete, interior work for tenants remains, and the official opening of the building has been delayed by the COVID-19 pandemic.
Designed for Key Development by Skylab Architecture, the building was engineered by catena consulting engineers. Anderson Construction was the general contractor. All the mass timber products were sourced within Oregon, primarily from DR Johnson Wood Innovations and Freres Lumber Company Inc.
The site of the 23,000 sq ft Sideyard building was “city land, leftover from [a] roadway reconfiguration” near downtown Portland and “considered of no value,” explains the Skylab website. The property also features a roughly 10 ft change in elevation from the higher, eastern side along Couch Street to the lower, western edge on Third Avenue, notes Jason Thompson, P.E., S.E., LEED AP, a catena principal. Couch Street curves westward around the southern end of the site, passing over Third Avenue before merging into Burnside Street, which leads to the Burnside Bridge that crosses the Willamette River. Roughly wedge-shaped in plan, the Sideyard building follows the contours of its site, measuring roughly 153 ft long in the north-south direction and a maximum of 56 ft wide in the east-west direction — a design that “maximizes the use of the site but also creates this interesting, aesthetically pleasing shape,” Thompson says. Because of the elevation change, the building’s ground floor level is located below grade on its eastern side but at grade on its western side, which means the facility features two main entrances at two different levels — one on Couch Street and the other on Third Avenue.
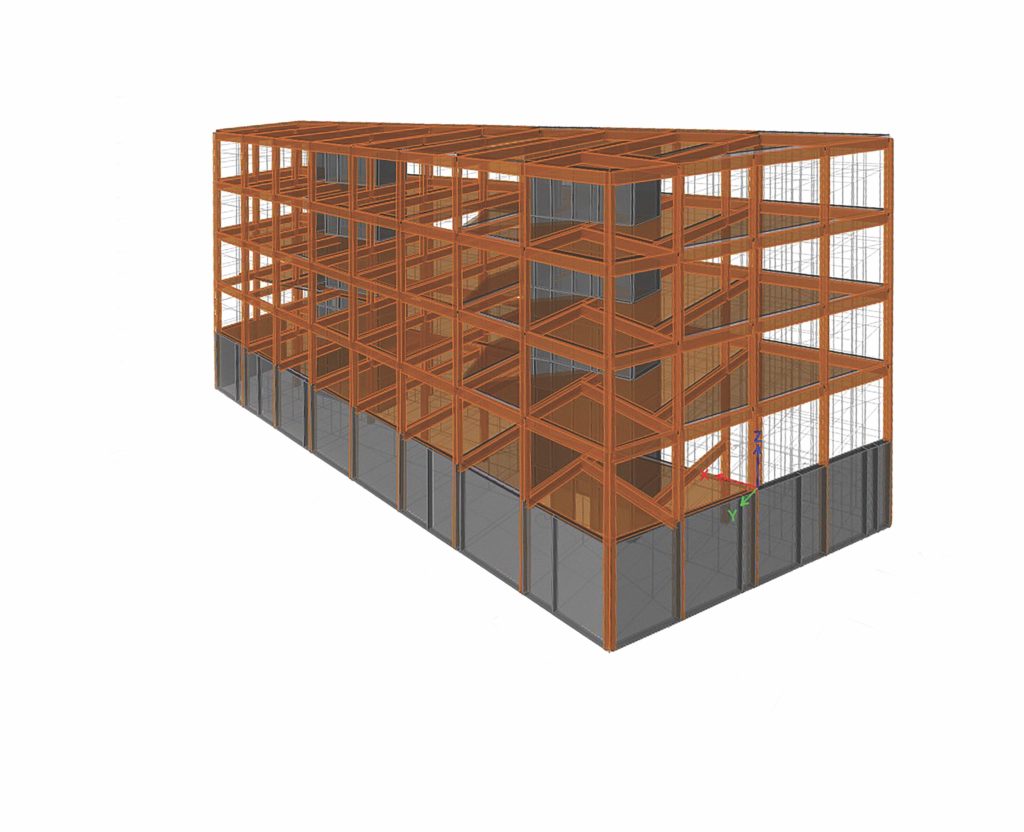
Although the building’s structural framing relies primarily on mass timber, steel elements were used as connectors and supports for the timber products. The foundations consist of shallow, reinforced-concrete footings, and there are two reinforced-concrete cores to accommodate the Portland region’s high seismicity, Thompson says. The building facade features masonry veneer cladding with light wood-framed walls as backup and extensive glazing — the windows measuring as much as 17 ft wide and more than 10 ft tall.
Catena was selected for the project because of the firm’s experience with designing mass timber structures, says Thompson. The Sideyard building features cross-laminated timber panels for its floor and roof decking and glue-laminate timber for the columns and beams, all supplied by DR Johnson. The project also made “innovative use” of a new mass timber product from Freres known as mass plywood that Thompson describes as “plywood on steroids.” Mass plywood was used for the wooden stair systems in the two cores, forming the treads, landings, and a center wall used to support the stairs. Mass plywood “really threw the city for a loop as far as their jurisdictional review because they were unfamiliar with the product,” Thompson notes. But through reports and tests, Freres was able to demonstrate the capacity of the panels, “so we were able to get those approved,” Thompson notes.
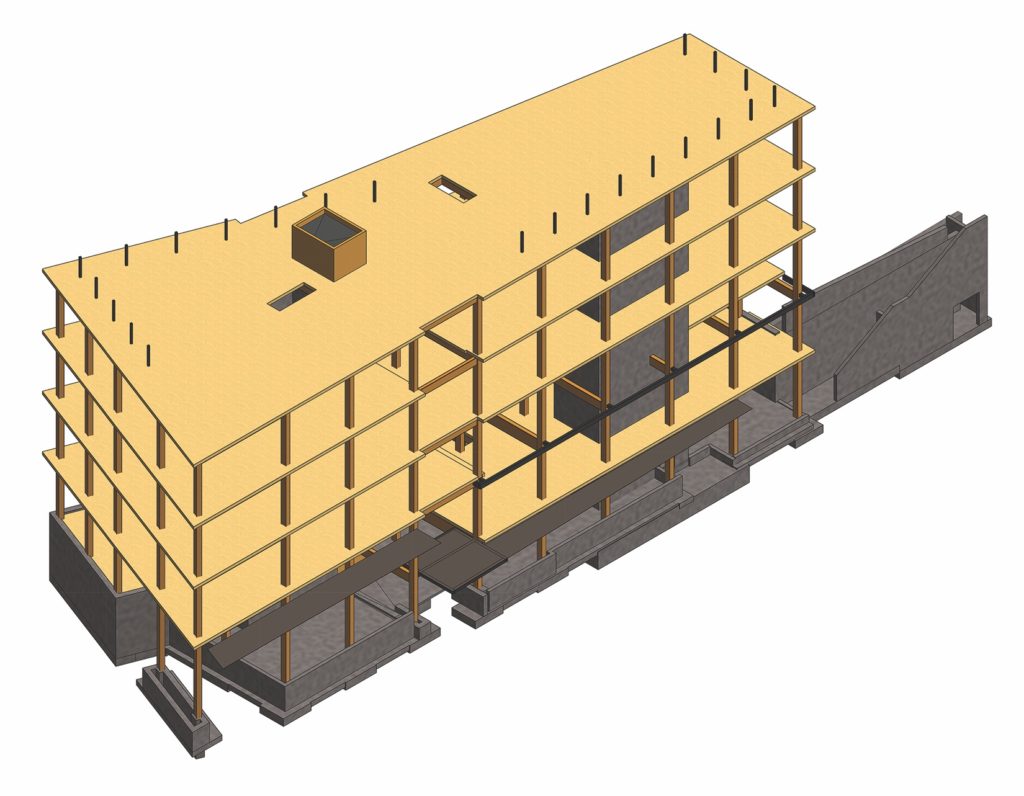
The building also features one elevator located outside of the northern core. Although originally designed with concrete walls, the elevator shaft was ultimately constructed with standard wood stud-framed bearing walls that feature drywall inside and outside the shaft, Thompson says.
Ironically, although the site of the Sideyard building had previously been used as a staging area for construction material on other nearby projects, the Sideyard project itself had little available space to stage its materials, Thompson notes. Fortunately, the prefabricated nature of mass timber means that “when it’s delivered, it’s ready to be erected right away,” Thompson says. The contractor would “have a truck come in with the glulam columns, for example, and those columns were precut and any hardware for connections … had already been preinstalled in the shop. So all they had to do was pick those pieces off the truck with a crane and immediately set them into place.”
The Sideyard building’s glulam columns measure 10.75 by 13.5 in. in cross section, and the horizontal glulam beams vary in size, from 6.75 to 8.75 in. wide and from 19.5 to 27 in. deep. The largest beams are used on the second level to help support the increased live load requirements of that floor, which features a 4 in. thick concrete topping above the CLT decking, Thompson explains. The beams connect to the columns through steel hardware — manufactured by Knapp AG, of Graz, Austria — that is completely concealed within the mass timber material, “so it looks as if you just have the ends of the beams dead-ending into the face of the column without any means of connection,” Thompson says.
The project also made “innovative use” of a new mass timber product from Freres known as mass plywood that Thompson describes as “plywood on steroids.”
The irregular, nonorthogonal footprint of the building required a range of five-ply CLT panel sizes, up to 10 ft wide and nearly 40 ft long and typically just under 7 in. thick. The panels are supported by the glulam beams, which are typically spaced 14 ft, 8 in. on center.
Fire safety is always a primary concern when designing wooden structures. For the Sideyard building, the glulam beams and columns and CLT panels had to maintain their load-bearing capacities when subjected to one hour of charring without losing more than 1.8 in. of material on the bottom and sides of the beams and on all four sides of the columns as well as 1.5 in. at the beam-to-column connections, Thompson says. Some beams required double connectors to accommodate the expected loads at the ends of the beams, which in turn required the larger, 8.75 in. wide beams to maintain the required connection char depth, Thompson notes.
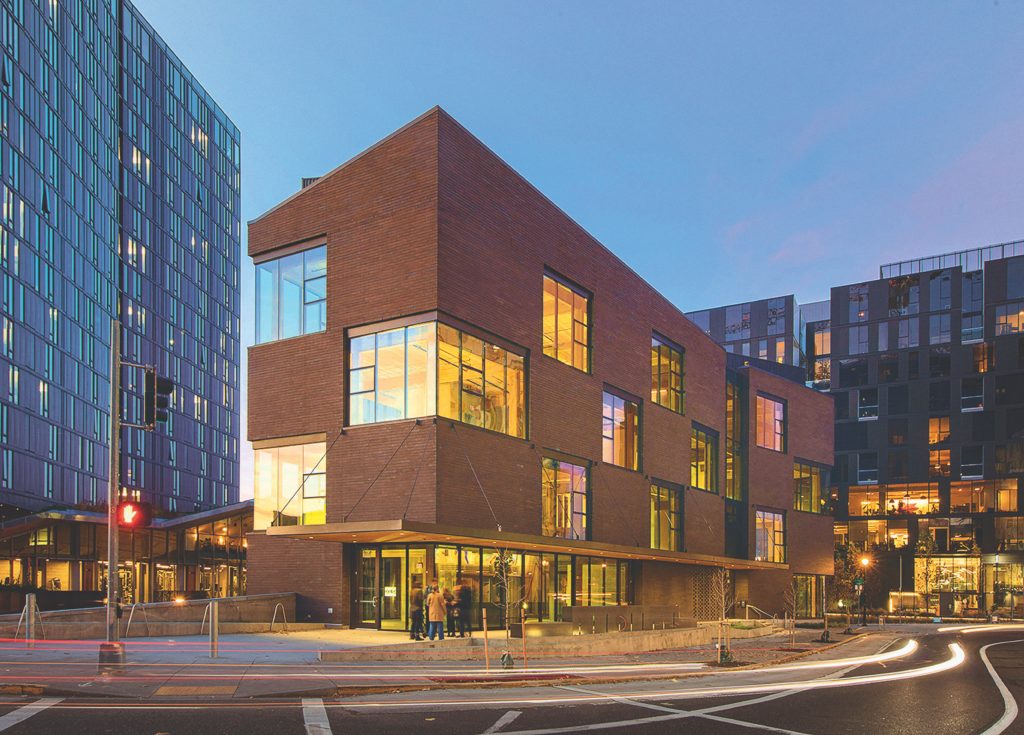
The Sideyard building’s concrete foundations include large, mat-like footings beneath the cores that measure as much as 40 ft long in the north-south direction and roughly 26 ft long in the east-west direction. The core shear walls measure 10 in. thick and serve as the building’s primary lateral force-resisting system, says Thompson. Inside the cores are the mass plywood stairs that include a 7 in. thick central spine wall, 3 in. thick stair treads, and 7 in. thick landings, Thompson says. Because the CLT deck panels are designed to behave as a diaphragm and transfer seismic loads to the cores, individual panels are in some cases secured together with steel straps roughly 2 in. wide and 0.75 in. thick. Together with screws, the straps are designed to help the panels “behave more as a monolithic material, panel to panel” during seismic events, Thompson says.
Threaded tension-only steel rods and steel beams connected to the glulam beams support a steel canopy on the building’s eastern facade. Brick-clad parapets line the roof perimeter, supported by light wood framing and periodic diagonal braces. Steel-framed screening, inset from the parapets, shields the rooftop mechanical systems.
The Sideyard site includes a new public plaza along the Couch Street side of the property, and a new set of concrete stairs will lead down from Couch Street to Third Avenue to improve pedestrian connectivity. These amenities required the construction of a new concrete retaining wall, roughly 12 ft tall, without compromising the existing structural support of the Burnside Bridge abutment provided by a preexisting, shorter retaining wall just to
the east.
This article first appeared in the October 2020 issue of Civil Engineering.