Researchers at Brown University have developed a new method of making metals harder: compressing them. Hitting chunks of metal with a hammer is a longstanding technique for hardening the material. Metallurgists can also bend, twist, or run metal between rollers to strengthen it. Each of these methods breaks up the metal’s grain structure, which features microscopic crystals. The smaller the grains, the harder the metal.
Called top-down methods, those older approaches make it difficult to control the size and shape of grains that result, notes Ou Chen, Ph.D., an assistant professor of chemistry at Brown and the corresponding author of a paper on the new research. Instead, Chen and his colleagues developed a bottom-up method using pressure sintering that compresses together the individual nanoclusters of crystals to form macro-scale chunks of solid metal that have proved to be much harder than naturally occurring metal structures, according to a Brown press release on the research. Using the bottom-up method, which involves both a chemical treatment and the application of pressure, “we can more perfectly control the particle size” as well as the shape and morphologies of the particles, Chen explains.
A paper on the research, “Bulk Grain-Boundary Materials from Nanocrystals,” appeared in the Feb. 11 issue of the journal Chem. The term grain boundary refers to a range of chemical, physical, and mechanical material properties, such as ductility, catalytic ability, and thermal and electrical conductivity, according to the Chem paper.
Applying pressure
Using the new process, the researchers produced small coinlike objects made from nanoparticles of gold, silver, palladium, and other metals. Gold “coins” 0.6 cm in diameter turned out to be two to four times harder than standard gold metals but with electrical conduction and light reflectance properties that were “virtually identical,” the press release noted. The technique should work for any metals and even alloys, Chen adds, and can be scaled up to much larger materials. “There is no operating end” to the size, Chen says.
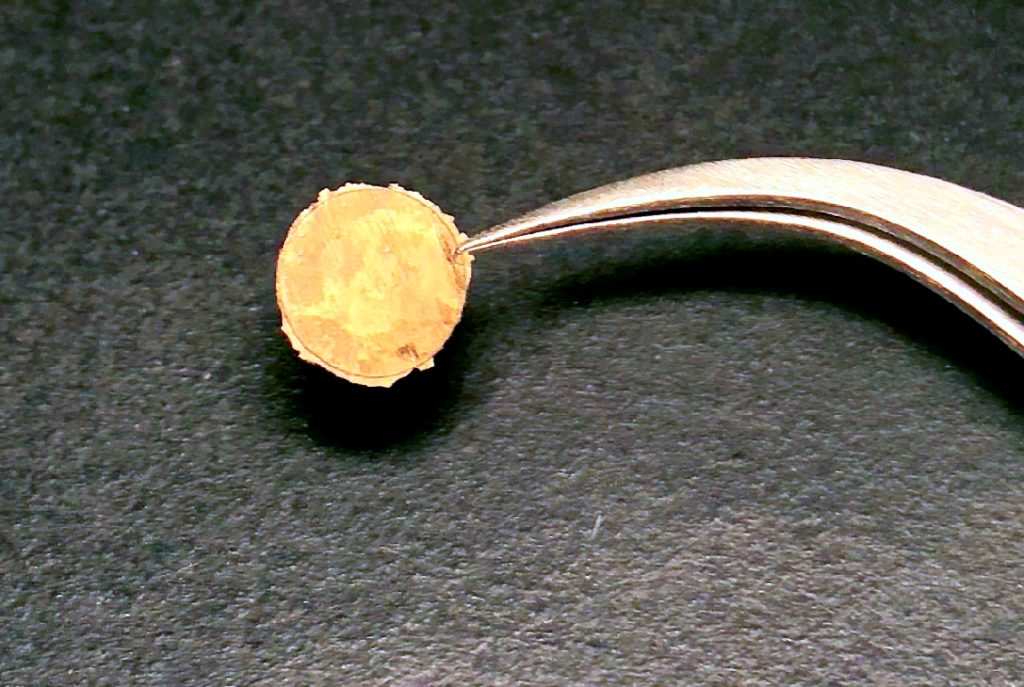
The process begins with a chemical treatment for the nanoparticle building blocks that is designed to “wash away” the ligands on the metal nanoparticles, which are organic molecules that typically prevent the formation of metal-to-metal bonds, Chen explains. By stripping away the ligands, the clusters of “bare” nanoparticles can better fuse together under pressure.
In the recent research that produced the gold coins, a homemade piston cylinder applied 0.6 GPa pressure for approximately 10 minutes to reduce any void spaces within the material, Chen notes. The technique can be used to produce bulk metals of various sizes, shapes, and compositions, according to the research paper.
Although the technique has so far been used primarily with flat surfaces, other approaches could involve lasers to apply uniform pressure and fuse nanoparticles along curved surfaces, Chen notes.
Making metallic glass
The Brown process has already been used to create an exotic form of metal known as metallic glass. It is a material that “many researchers and industry players believe … will one day replace plastic and metals in many applications,” according to a press release from the University of Oregon, where researchers are also experimenting on the material.
Metallic glasses are amorphous, which means “they lack the regularly repeating crystalline structure of normal metals,” noted the Brown press release. This “gives rise to remarkable properties,” the release continued, that make metallic glasses much stronger, more crack-resistant, and more easily molded than traditional metals. They also exhibit superconductivity at low temperatures.
Although most metallic glasses are made from alloys, Chen and his team produced a metallic glass from a single component — in this case, amorphous palladium nanoparticles. It is believed to be “the first example of single-component bulk metallic glass generated under nonharsh conditions,” noted Chen and his colleagues in the Chem paper.
Pushing the method
Because the Brown process produces free-standing grain-boundary materials without the need for substrates, the approach should help fabricate a variety of grain-boundary materials “that cannot be easily produced by existing techniques,” according to the Chem paper. The authors also explained that the new process can be applied to “other materials systems and on much larger production scales.”
More research is needed to “see how much further we can push this method” to wider applications, Chen says. But he is optimistic that it could result in commercial products within a few years. The process should be able to produce large industrial components or super-hard metal coatings that can be added like a film to harden existing materials.
The research has been patented, Chen adds, and he “looks forward to collaborating” with civil and structural engineers on potential applications.