Traditional thinking may have you believe that site built structures are the best solution for resilient need applications. That may be true in some very specific cases where extremely thick reinforced poured concrete shells are required, but not in most. Plant manufactured precast concrete panelized buildings can provide all the security, durability, and customized versatility engineers require, with a more competitive bottom-line and shorter completion schedules. And as far as outperforming wood, metal, and masonry structures, there’s very little argument.
What are Easi-Set Buildings?
Easi-Set and Easi-Span Precast Concrete Buildings are ideally suited for a multitude of market applications. Licensed producers working all across North America install single buildings, as well as work on design build teams to complete entire complexes and large scale infrastructure projects. Precast buildings can be customized to meet exacting specifications and are engineered to be resistant to inclement weather, vandals, fires, floods, blasts, UL 752 Level 5 ballistics, and even corrosive environment.
Easi-Set Buildings set a standard
• DURABLE – Engineered to last through decades of hard use with little maintenance
• SECURE – The simplest, easiest method to harden your infrastructure
• FAST – Shave weeks or months off your timelines
• ECONOMICAL – Savings in design, site preparation, site impact, labor and schedules
• VERSATILE – Easily design structures as small as generator shelters to 50’x250’x35’ clear-spans
Here are four examples showing the versatility of precast concrete buildings:
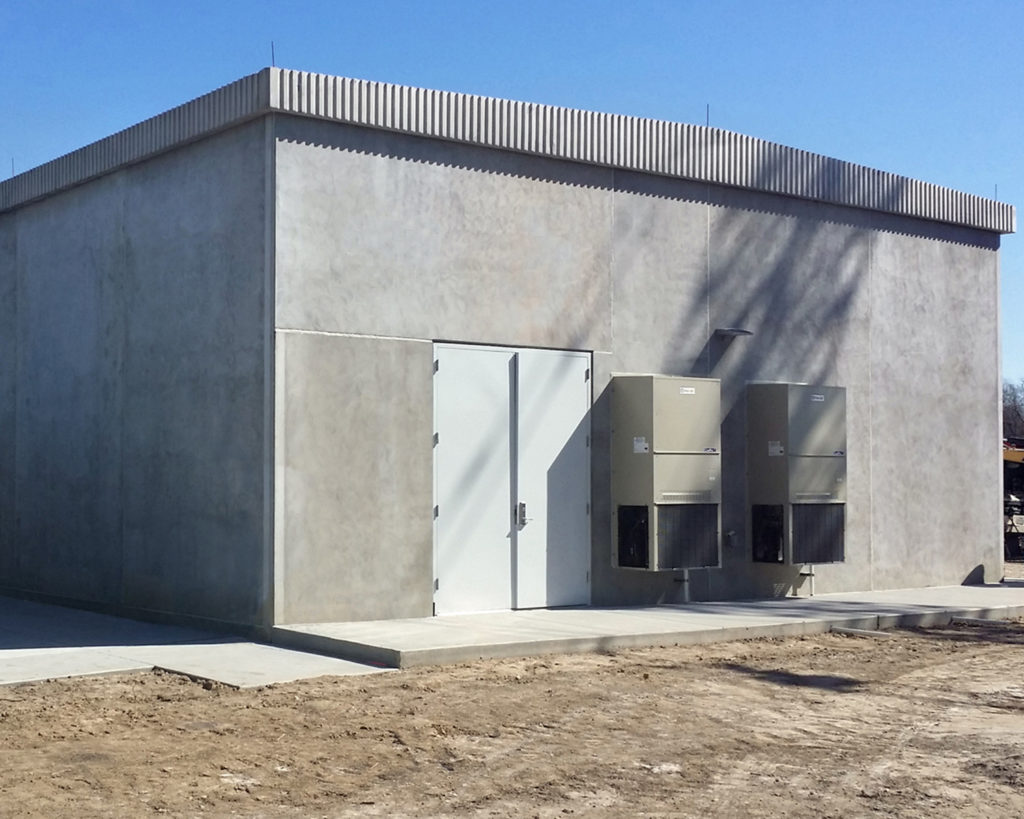
Case Study – Water Treatment Pump Station Installation
The Cost and Time Savings of Precast Concrete Buildings
When the time frame for the project was too short for traditional construction methods, the San Jacinto River Authority turned to a precast concrete building solution for their pump station install in Baytown, Texas.
The original specification was for a large concrete masonry unit building. Houston contractor Boyer Inc. was the low bidder on the project, but its bid was over budget. Through value engineering, Boyer offered Easi-Span Precast Concrete Buildings produced by Lonestar Prestress as an alternative. Nathan Davis, a project manager for Boyer, said the building was an easy aspect to quantify. “There were not only savings on the front end for cost of the structure, but there were savings on the back-end with the reduced time from pouring the slab to setting the roof panels that allowed Boyer to reduce overall construction time, labor and equipment costs for the project.” Davis noted, “The offsite fabrication of the wall and roof panels was timed so that once the slab was poured and cured we could set the panels.”
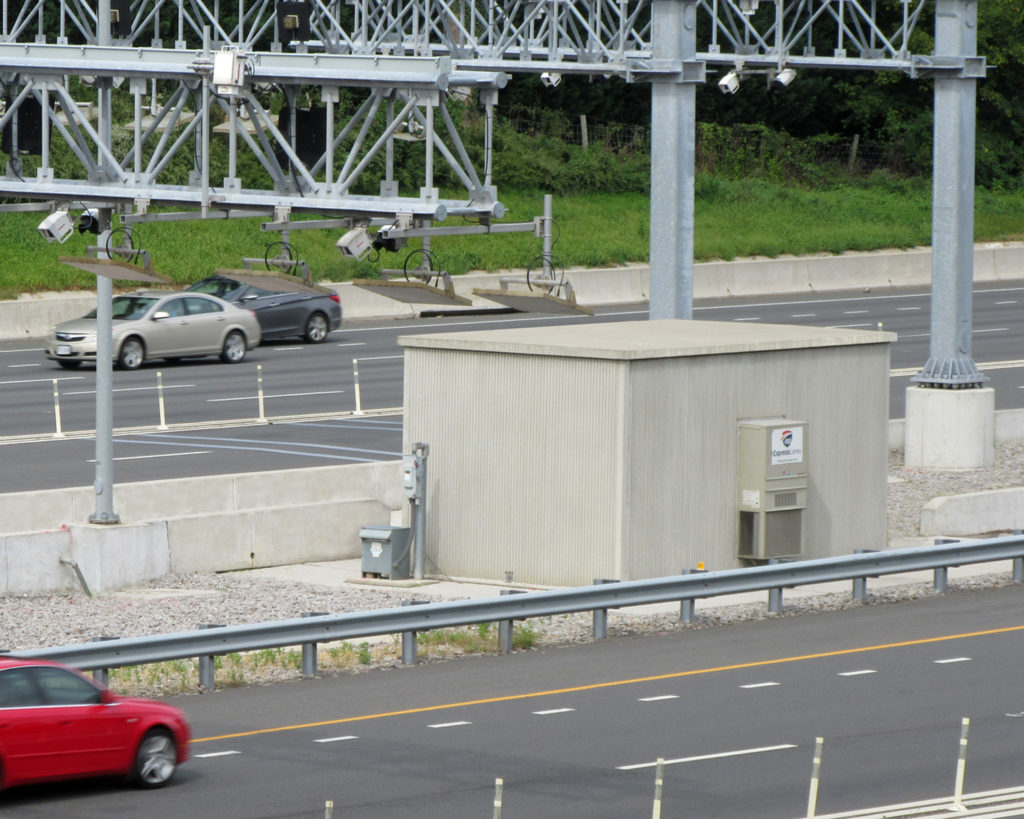
Case Study – Highway Toll Lane Equipment Buildings
Securing the future of an Iconic American Beltway
A consortium, Capital Beltway Express, was established to design, build, operate, finance and maintain a $2 billion Express Lanes project located on the Beltway that has encircled Washington DC since the 1960s. The 495 Express Lanes were the first of its kind to provide HOV service on the Capital Beltway – as well as the option for travelers to pay a toll for a faster and more predictable trip using EZ-Pass.
Construction, managed by Fluor-Lane, began with two new lanes in each direction on a 14-mile stretch. Flour-Lane contracted with Easi-Set producer Smith-Midland Corporation to manufacturer and install 10 technical shelters to securely house all the E-ZPass recognition equipment. All along the 14.5 mile corridor the Easi-Set all-precast concrete buildings were set in the median strip next to two sets of information collecting pole assemblies hanging over both sets of opposing Express Lanes. Use of this system allows for the EZ-Pass system to collect the tolls without any slowing of traffic flow. Smith-Midland manufactured all of the 4” thick reinforced precast concrete panels at their Midland, VA plant, then shipped and erected the buildings using an on-site crane. Each building was set and ready for final equipment outfitting in just one day. This saved valuable time for Flour-Lane, as well as keeping the work site free from weeks of on-site workers needed by traditional site built construction methods.
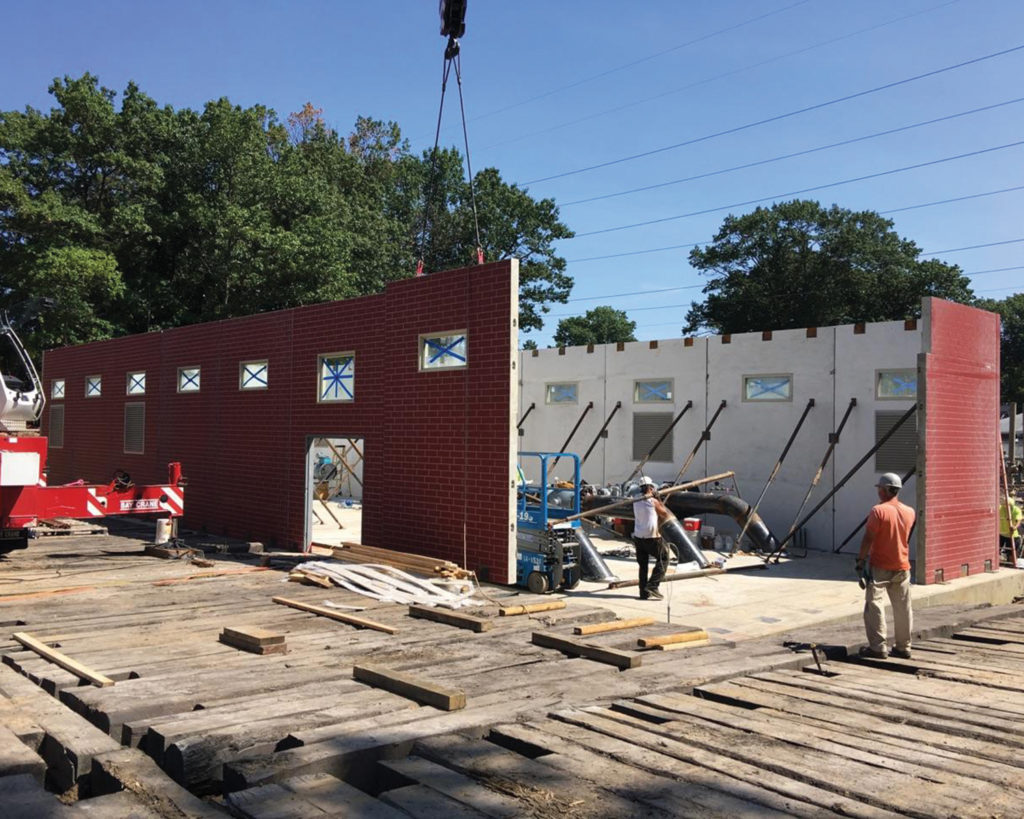
Case Study – Gas Pipeline Building
Easi-Set Building Producer Delivers for Major East Coast Utility
Public Service Electric & Gas (PSE&G), New Jersey’s oldest and largest regulated gas and electric delivery utility, set out to upgrade and enclose its metering and regulating station in Sayreville, N.J. Because the facility is located in a residential neighborhood, it was important to create a strong, low-maintenance building with visual appeal. An Easi-Set precast concrete building was recommended by HMI Technical Solutions LLC.
The design centered around providing a 30’ x 80’ x 15’ Easi-Set Building consisting of twenty-two 10’ wide x 15’ high concrete wall panels and eight 10’ wide x 31’ long tapered concrete roof panels.
When the panels were ready, they were delivered and installed in just 10 days around the already completed slab and equipment.
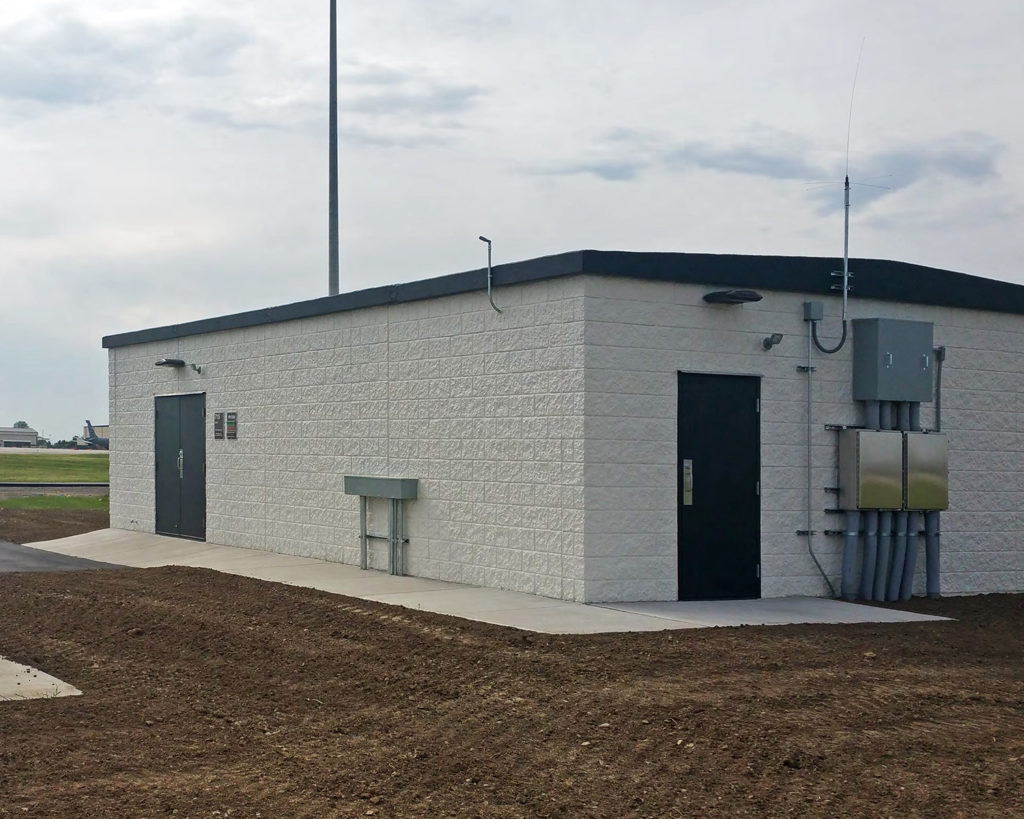
Case Study – Airport Runway Equipment Building
A Strong Building Solution for a Secure Military Base
The open airfield at Grissom Air Reserve Base in Kokomo, Ind., leaves vital Air Force equipment vulnerable to potentially damaging winds. The area has historically been subjected to straight line winds over 100 mph and strong Midwest tornadoes reaching 150 mph. When the base needed a Ground-Air Transmit-Receive (GATR) building to house new communication equipment, a rugged solution was the only option to withstand such weather conditions. The remedy was found with an all precast concrete building from Easi-Set Buildings manufactured by McCann Concrete Products Inc., Dorsey, Ill.. “The flight line in which the building is placed is wide open, allowing for exceptionally strong winds,” says Richard Sparks, a project manager with Federal Construction Group. “Since the structure houses sensitive communications equipment, something extremely solid was needed to fit the bill, and precast concrete was the perfect answer.”
To read the complete stories on these four case studies plus eight more, click here: https://precastbuildings.com/images/members/logos-graphics-brochures/Versatility_-_Easi-Set_Buildings_Case_Studies.pdf
To learn more about specifying all-precast concrete Easi-Set or Easi-Span Buildings, find your closest licensed producer, or get a no-obligation quote for your next project, call (866) 252-8210 or visit www.EasiSetBuildings.com.
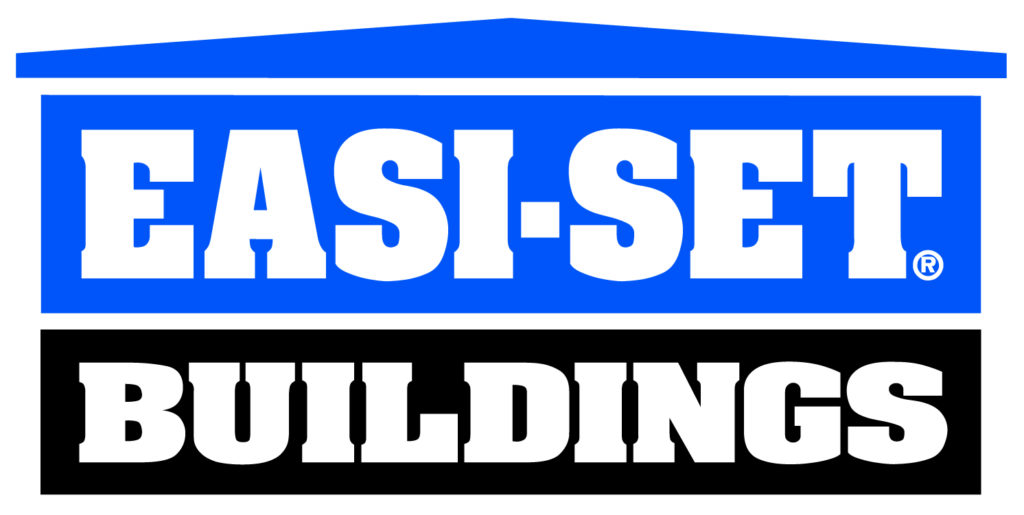