New York City’s new arts center, The Shed, features a 120 ft tall, steel-framed shell clad in translucent cushions that rolls out from around a fixed building to cover the adjacent public plaza, creating an enclosed space for concerts, performances, and other cultural events. The moving shell weighs approximately 8 million lb yet is supported at just six points by large-diameter steel wheels. Part of the city’s Hudson Yards development, The Shed was designed and constructed through a collaborative process seen as the future of engineering innovation.
New York City is often seen as a metropolis in motion, the proverbial city that never sleeps, its streets filled with vehicles, its sidewalks crowded with pedestrians, trains racing through underground tunnels and along elevated tracks. So it is probably fitting that one of New York’s newest cultural attractions is also a massive structure that moves.
Known as The Shed, the 200,000 sq ft facility is located on West 30th Street, between 10th and 11th avenues on Manhattan’s west side. Owned by a nonprofit cultural organization of the same name, The Shed features two steel-framed structures: the so-called fixed building, which is stationary and features four double-height levels of galleries, a theater, rehearsal spaces, and other arts-related amenities, and the 120 ft tall movable shell that normally wraps around the fixed building on the northern, southern, and eastern sides. When desired, the shell portion can roll out from west to east on enormous wheels and rails to cover a 20,000 sq ft public plaza, creating a massive climate-controlled space for performances, installations, and other events. The Shed can accommodate up to 3,000 attendees when the spaces within the shell and the fixed building are combined.
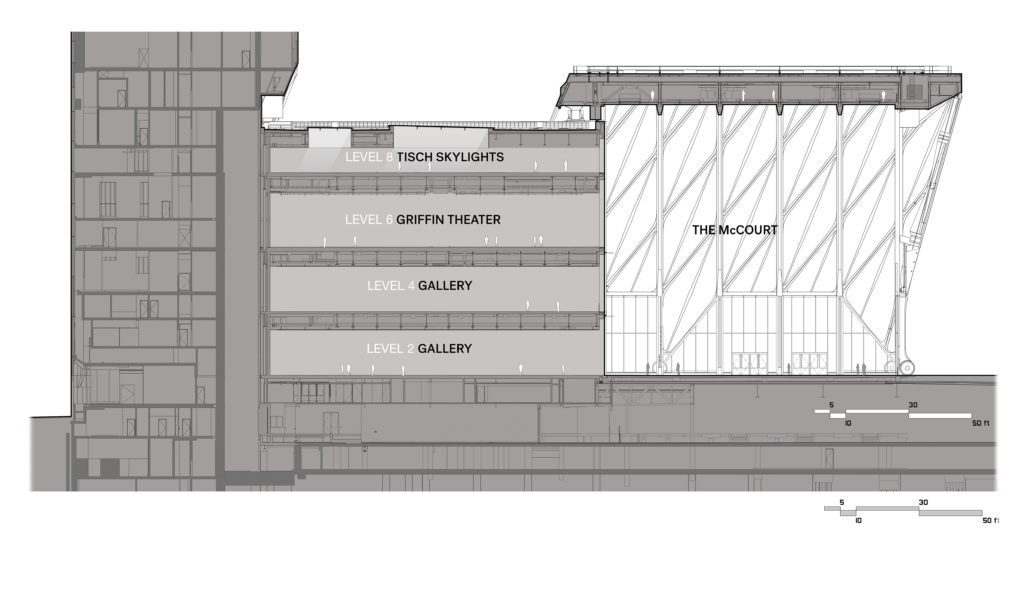
The Shed is one of the key public amenities within the Hudson Yards development, which at more than 18 million sq ft of commercial and residential space is the largest private development in New York City’s history. Many of Hudson Yards’ commercial properties — and a portion of The Shed — are supported on a 424,000 sq ft steel and concrete platform that was constructed above an active rail yard, which enabled the trains to remain in operation throughout the construction phase. The Shed itself is nestled into the lower part of one of the Hudson Yards’ residential towers, the 88-story tall 15 Hudson Yards. The two buildings share service and freight elevators but are independent structures, separated by an expansion joint, notes Scott Lomax, CEng, a senior principal and structural engineering practice co-leader with the international engineering firm Thornton Tomasetti.
Thornton Tomasetti was the structural engineer for both The Shed and the Hudson Yards platform. The firm designed the public plaza that the moving shell covers and, among other services, was responsible for the facade engineering, construction engineering, and kinetic engineering that moves The Shed’s shell back and forth. The firm also served as the structural engineer for two of the Hudson Yards towers, a large sculpture, and the site’s retail component. Hardesty & Hanover was the mechanization design consultant on The Shed’s kinetic systems. Sciame Construction was the general contractor for The Shed, and Cimolai was the steel fabricator.
The Shed was designed by the architecture firm Diller Scofidio + Renfro, in collaboration with the Rockwell Group; both firms also designed 15 Hudson Yards, in collaboration with Ismael Leyva Architects. WSP was the structural engineer of 15 Hudson Yards.
Completed in 2019, The Shed closed temporarily during the COVID-19 pandemic; however, it reopened last month under certain health and safety restrictions.
The design and construction of The Shed required extensive collaboration, sharing of information, and a willingness to work outside traditional boundaries of knowledge and expertise — an innovation of the process involved rather than just the products installed, says Tom Scarangello, P.E., M.ASCE, the executive chairman of Thornton Tomasetti. “People think innovation is just a new product,” Scarangello explains. “But what really drives innovation in engineering is the idea of changing the process, and The Shed is a perfect example. It was a process that started with a blank sheet of paper — a mandate from the city and the state as part of the Hudson Yards development program to have an iconic cultural institution at this location.” That mandate required bringing “all kinds of capabilities to the table,” Scarangello notes, pointing out that while Thornton Tomasetti has its own kinetics group, the project was best served by adding expertise from Hardesty & Hanover, “a world leader in movable bridges and movable structures … who could take (the project) to the next level along with us.”
During the roughly decadelong design and construction phases of The Shed, Thornton Tomasetti and Hardesty & Hanover even shared a key employee. Thomas A. Duffy, P.E., now a Thornton Tomasetti principal and the firm’s project manager on the kinetics portion of The Shed, was originally Hardesty & Hanover’s project manager, before changing firms in 2012. In his new role, Duffy focused on making certain that the structural and mechanization systems were well coordinated “because that’s typically where we’ve seen trouble” on similar projects, he notes. Too often, Duffy explains, there is little collaboration between the structural and the kinetic engineers, so that was something he helped make sure “did not happen on this project.” When Thornton Tomasetti would go into a project meeting with the architects, it helped to have access to Hardesty & Hanover’s detailed mechanical and electrical expertise. Likewise, Thornton Tomasetti could use its expertise and experience to “translate” what the architects had discussed to ensure the interface worked well with Hardesty & Hanover, Duffy says.
What made work on The Shed fascinating, Lomax adds, was how the project combined so many challenges. Any two or three of those issues might have happened on a more traditional project, he says, but on The Shed, they all had to be resolved within the same facility at the same time. In addition to everything involved in the moving shell, Lomax explains, there were also several enormous operable walls in both the shell and the fixed building. There were long-span spaces and double-height clear spaces. The cladding of the shell featured giant ethylene tetrafluoroethylene (ETFE) cushions — some nearly 70 ft long — while the fixed building had a cantilevered glazed facade on one side. Also on the list were issues with integrating the mechanical, electrical, and plumbing systems into the structural framing; questions over stiffness versus weight in the overall structure of the shell; concerns about wind-induced deflections; safety considerations, given that the shell’s steel framing, the wheels, and the rails were all exposed to the public; and phasing, scheduling, and procurement issues that had to be resolved to avoid delays.
Comparing The Shed to both a Swiss watch and “a piece of sculpture that moves,” Duffy stresses that precise, early, and ongoing communication with fabricators, erectors, and suppliers about the sometimes extremely tight tolerances and other unique issues involved in the design and construction of The Shed was essential to the project’s success. “You couldn’t bid this out as a typical project,” he explains.
Although a small portion of The Shed is supported on the Hudson Yards platform, most of the facility is founded on other concrete and steel structures — for loading docks, parking facilities, and other spaces — separate from the platform but also part of the overall Hudson Yards development, Lomax says.
The fixed building — branded as the Bloomberg Building, after former New York City Mayor Michael Bloomberg, a donor — features steel-braced framing with 100 ft clear spans in some of the gallery spaces. Those long spans are supported by plate girders 5 ft deep and castellated to reduce weight and provide openings for the mechanical systems. The preset castellations helped avoid delays during the construction phase since the steelwork was designed before the mechanical systems had been finalized, Lomax says. Castellated supports “gave us a lot more flexibility to accommodate changes in the final design of the mechanical systems.”
The south side of The Shed property overlooks the High Line, New York’s former elevated rail system that was turned into a public park (see “New York’s ‘High Line’ Railroad to Become an Elevated Park,” Civil Engineering, July 2006, pages 14, 16-18). A glazed facade cantilevered roughly 15 ft off the main structure provides views of the High Line from the fixed building lobby, which also features a series of crisscrossing escalators. The lobby’s large span is supported by a 12 ft deep plate girder, Lomax says, while a torsion box system and a series of steel ribs support the cantilevered glazing. The facade features a cable tension system in which the primary elements supporting it are cables, which creates an elegant system with minimal structure, Lomax says. The system requires anchorage to a stiff supporting structure so that the cables are tensioned against something.
To create a column-free circulation space, the cable wall in the fixed building is supported by a structure that is cantilevered from a supporting structure (the long-span torsion box), which is set back from the facade itself. A cable wall in itself is a complex balance between supporting structure and facade system, Lomax adds, and to do this from a cantilevered structure increases the technical difficulty of the challenge. But it created a beautiful facade system and unrestricted vertical circulation space, he says.
The movable shell — which, when extended over the plaza, is branded as the McCourt, after donor Frank McCourt — is formed from a steel diagrid that was carefully designed to be both stiff and lightweight, with elements that include a 30 in. deep trapezoidal box system and plate thicknesses that vary from 0.625 to 2 in. Even so, the overall shell weighs about 8 million lb, all of which is supported at just six points — the six assemblies of wheels and axles, called bogies, that roll along the 273 ft long rails, notes Brian Hamill, P.E., M.ASCE, the chief engineer of Hardesty & Hanover’s kinetic systems group.
There are 16 wheels in all, each 6 ft in diameter. Four wheels are located at each of the two bogies on the eastern, leading end of the shell plus two wheels on each of the other four bogies located along the northern and southern edges of the moving structure, Hamill explains.
Although the systems that help move structures are often concealed from view or located in spaces that are inaccessible to the general public, The Shed took a different approach. Somewhat uniquely, key aspects of its kinetic system are located at ground level, in full view of visitors and passersby. “So we had to rethink what that interface (of the wheels and rails) looks like when you’re in the middle of a public plaza and people can go up and touch the wheels,” Duffy explains.
An early concept for the system considered placing the rails and wheels below grade, Hamill adds, but there was not sufficient depth, given the Hudson Yards facilities located directly beneath The Shed site.
The motors and other machinery that make the shell move are located atop the fixed building. The design team considered various types of kinetic systems, including a rack-and-pinion system, a wire rope system with drums and steel cables, and a telescoping hydraulic cylinder system. “By far, the rack-and-pinion system was superior,” Duffy says, because of such factors as the positive control of the moving system, regardless of wind speed or direction, and easier long-term maintenance. The system includes a built-in anemometer, Duffy adds, and the operational wind speed for opening or closing the shell is capped at 35 mph.
The system features two sleds that operate on tracks secured to the top of the fixed building roof. “Each sled is supported on rollers and includes six-gear pinions that engage gear racks installed on either side of the tracks,” explains Hamill. “There are three pinion gears on each side of the sled engaging a rack. The pinion gears are mounted on the output shaft of a planetary gear reducer which is in turn driven by a 15 hp electric motor. When the motors are running, the pinions rotate and drive the sled in either the extending or retracting direction.”
There are six 15 hp motors on each sled for a total of 90 hp per sled, Hamill adds. Each sled is connected to a link on the underside of the shell roof. “As the sled moves along the track, The Shed shell moves along with it,” Hamill says, adding that the two sleds are synchronized electronically to move in unison to keep The Shed shell moving in the proper orientation with the rails down at plaza level.
The operation of the shell can be controlled from a panel on top of the fixed building — within sight of the rack-and-pinion interface — or by a wireless system that an operator can use from the plaza, to watch the action from ground level, Duffy says. Prior to moving the shell, trained operators will first examine the rails and the rack-and-pinion system, checking for cleanliness, making sure there is no built-up corrosion, and ensuring that everything is properly lubricated. A security perimeter will be established at ground level to ensure that no one gets too close to the rails or wheels while they are in motion, Duffy adds.
Moving at roughly 25 ft per minute, it takes the shell approximately five minutes to open or close — somewhat slow compared with the 60 ft per minute speeds of other movable structures, such as retractable stadium roofs, says Hamill. But speed is not as essential for The Shed’s movements, which can be scheduled well in advance, as it is for the impromptu opening or closing of a stadium roof that might require a delay in an ongoing event, he explains. A faster speed can also involve larger, more expensive equipment, which would have made it more challenging to fit everything onto the roof of the fixed building, where there were other systems and services planned, Hamill says.
Despite its many unconventional aspects, the project also relied extensively on conventional materials and components — while pushing the boundaries on various aspects, says Lomax. These included the rails for the shell, which were the largest commercially available rails on the market, procured from a steel fabricator in Belgium — an ArcelorMittal plant — that only rolls out that product once every two years, notes Duffy. Fortunately, Hardesty & Hanover had worked with those rails on other projects and therefore knew about the long lead time, Duffy adds. Moreover, Thornton Tomasetti had been involved in The Shed project from conceptual design, which meant it was well aware of what was needed and by when. Together, the two firms ensured that the project would “get on that fabrication and delivery schedule to get the amount of rail we needed in time,” explains Duffy, who adds that the rails were one of the first parts of the overall kinetic system to be installed.
The wheels that run along the rails, however, were customized because “we were literally off the charts” when it came to the loads that would be imposed, Duffy adds. The loads and other requirements for The Shed wheels were somewhat similar to those of large container cranes at shipyards, Hamill says, “but we were actually well beyond even what the cranes use.” As a result, “we had to do quite a bit of calculation about the geometry of the wheels, the interface with the rails, the hardness of the heat-treated steel,” and other aspects, Hamill says.
By increasing the wheel diameter, however, the design team was able to reduce the contact stress between the wheels and the rails, “so we wound up with custom-designed 6 ft diameter wheels … to keep those stresses in a manageable range,” Duffy explains. “By using our engineering judgment and extrapolating from existing technology, we came up with something that we’re confident will last a very long time.”
Although there are seals that ensure a closed, climate-controlled environment inside the shell once it has rolled out over the plaza, the space can also become a sort of open-air pavilion when large operable walls are raised. There are eight such glazed panels — four on the east face and four on the north face — raised or lowered by a wire rope hoist system at the shell roof, says Hamill. The operable wall sections each measure approximately 35 ft tall by 25 ft wide and weigh approximately 35,000 lb. Jointly, they create an opening approximately 100 ft wide on their respective wall faces. An accordion-style moving wall within one of the fixed building’s galleries can also be opened to create nearly 30,000 sq ft of contiguous space for performances, concerts, and other events.
Because the ETFE cushions do not block light, the shell also features a series of full-height, deployable fabric shades that can be rolled down from the ceiling to the ground to create blackout conditions within the McCourt for performances. The shades also provide additional mass that helps with the space’s acoustics, Lomax says.
During the construction phase, the structure of the fixed building was erected first and then “we used it almost as shoring, as framing to create the deployable shell,” says Lomax. To complete work on the shell, that structure then had to be rolled out over the plaza — a process that involved about eight hours of moving the steel frame back and forth, at first just inches or less at a time, then longer and longer distances. Those small movements were attempted repeatedly and carefully monitored to make sure that everything was moving in sync, that the structure was not racking, and that the bogies were all moving at the same speed. “Over the course of the day, we built up moving the shell back and forth by these smaller amounts until we eventually moved it the entire distance — and it went incredibly well,” Lomax says.
Designed to be opened and closed as often as once a week, The Shed basically sat idle for months due to the pandemic. Hardesty & Hanover provided maintenance consulting services to the owners and was in contact with the facility’s maintenance team to discuss actions such as keeping the systems oiled and greased for long-term storage, notes Hamill.
Looking back at the long journey between the earliest discussions about a movable arts facility, which began around 2010, and the eventual completion of the dynamic structure, Thornton Tomasetti’s Scarangello says the innovations that made The Shed possible would never have happened if the design team had clung to a traditional approach “where everybody just did their own discipline and didn’t share and become knowledgeable about all aspects of the job.”
The architectural, engineering, and construction industry has long experienced any number of technological innovations, Scarangello adds, such as new materials and new systems. But “what our industry has lacked and what we’re excited about seeing” in projects like The Shed, Scarangello says, involves innovating the process. And that, he believes, “will change our
industry.”
PROJECT CREDITS Owner The Shed, New York City Architects Diller Scofidio + Renfro, New York City, in collaboration with the Rockwell Group, New York City Structural, kinetic, facade, construction, performance-based fire, and other engineering services Thornton Tomasetti, New York City Mechanization design consultant Hardesty & Hanover, New York City General contractor Sciame Construction, New York City Steel fabricator Cimolai, Porcia, Italy Steel rail fabricator ArcelorMittal, Luxembourg
This article first appeared in the November 2020 issue of Civil Engineering as “A Moving Sculpture.”
The cover photograph is by Iwan Baan, courtesy of The Shed.