London-based artist and designer Gerry Judah’s sculptures have earned a reputation the world over for fluid designs that integrate well into the landscape. Drift, a sculpture located between Dallas and Fort Worth, Texas, is one such sculpture that was installed in 2020. It boasts similar fluidity to some of Judah’s earlier designs, while presenting a 6.3 m high, 13 m long twisting, writhing silhouette all its own. (In Civil Engineering, see, for example, “Sculpture Pays Homage to the Written Word,” September 2019, pages 34-35, and “New Zealand Sculpture Reaches for the Sky,” April 2018, pages 24-25.)
With sculptures that appear as visually effortless as Judah’s, effective structural engineering must underpin the artwork. Hooman Baghi, CEng, associate director and structural engineer at the London office of Diales, designed and oversaw Drift’s engineering design. (Diales is a firm that primarily specializes in providing expert witnesses for the engineering and construction communities.)
To create the sculpture’s twists, 310 long steel blocks varying in thickness from 60 to 140 mm were stacked on top of one another at slightly varying angles. Commissioned by land development and property management firm Billingsley Company, the sculpture spreads its arms out horizontally with blocks decreasing in size as they get further from the center.
Overcoming challenges
Because the Drift members fan outward, vibrations were an important factor to incorporate into the structural analysis, Baghi says.
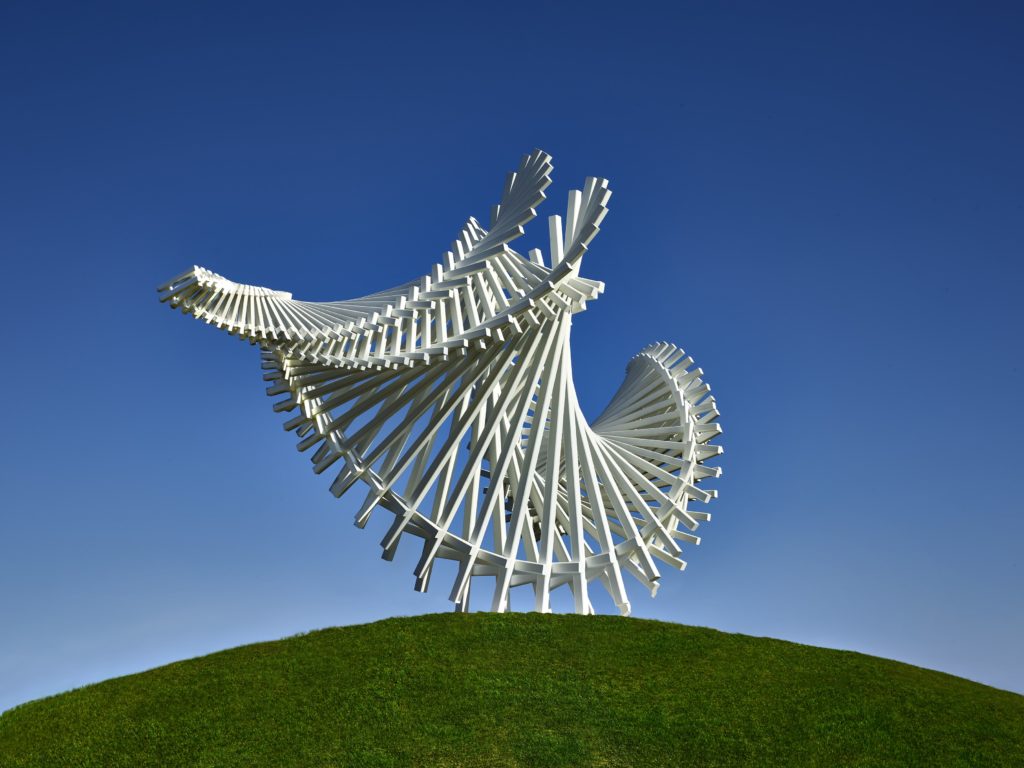
The sculpture’s location at the southern end of Tornado Alley meant the potential for high winds also had to be considered. “This particular sculpture had to be especially vigorously checked and designed,” Baghi says. The structural engineering team at Diales worked with Minimum Design Loads and Associated Criteria for Buildings and Other Structures (ASCE/SEI 7-16) for its wind and design load recommendations for the sculpture. The team determined that maximum wind speeds of 120 mph were possible at the site. Drift is designed to withstand those conditions.
“With any external actions such as wind, the outer part of the arms starts vibrating,” Baghi says. “As part of those vibrations, we get surface load distributions coming back to the base.” Additional factors to consider were the boundary conditions and fixity.
“The overall stability has been achieved by the fixity of the central part of the sculpture on top of the steel grillage foundation,” Baghi says.
The team had to figure out the dynamic performance and how to dissipate the vibrations and oscillations within the bolted, spliced connection joints. Every joint could be considered as a damper, Baghi says, distributing the vibration through local deflection and internal forces such as shear flow to the end of each section and moving it on to the next one like a relay race. Stiffer members in the middle are cantilevered coming out of the ground and compensate for twist. The stiffer units absorb the stresses and vibrations from the outer, smaller members’ deflections.
Because of the sculpture’s twists, the Diales team had to evaluate the effect of stresses induced by wind from various angles and four principal directions, in addition to the vertical.
Materials and modeling
Drift is constructed with mild 355 grade steel throughout. The team evaluated various materials for the structural units, including hollow beams filled with foam or light concrete. While Drift already weighs about 16 tons, heavier material was also considered.
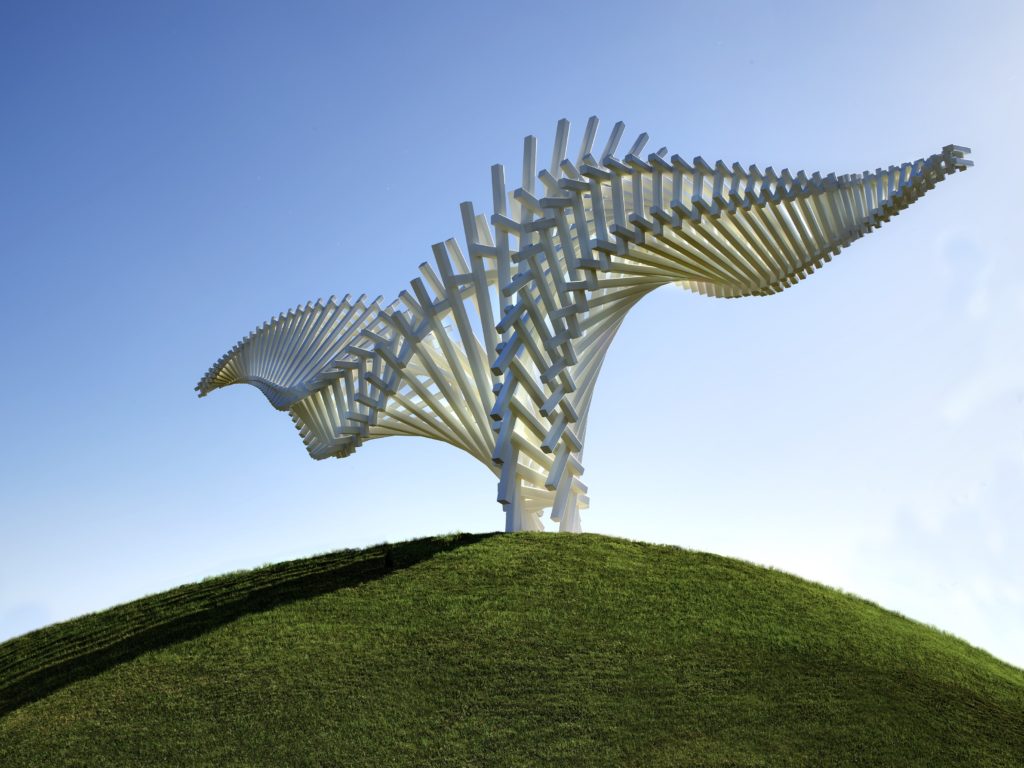
The team evaluated various possibilities using building information modeling and determined that mild steel, also known as low-carbon steel, was the best solution. Diales has developed computer modeling programs in-house, starting from sketches that are translated into nodes and translating all the elements into lines and shell elements as needed. After this, a structural analysis model is created, Baghi says.
Remote design
The sculpture was designed, engineered, fabricated, and painted in the United Kingdom, and then shipped to Texas for installation by a local team. Managing the project remotely was an additional challenge. “We didn’t have any control of installation, quality, and final finishes after all of the sections shipped to the U.S.,” Baghi says. “We had to have many trial-and-error runs on a computer model in the U.K. as well as a trial of assembly at the fabrication workshop at Littlehampton Welding just to ensure … (the members) fitted together when taken out of the box in the U.S.”
Because the final assembly was through bolted, spliced connections rather than welding together large segments, there was no room for even slight errors. “The fabricators at Littlehampton Welding who are experts in their field truly preserved the design intention,” Baghi notes.
The final piece “wonderfully bridges the gap between structural engineering and art,” Baghi says.