Until recently, the wastewater of some 320,000 people in the Greater Victoria area of British Columbia, Canada, was being discharged directly into the ocean after undergoing only the simplest of preliminary treatment. That all changed in December, when the new 108 ML/d McLoughlin Point Wastewater Treatment Plant began operations. The crown jewel of the Capital Regional District’s 775 million Canadian dollars ($605 million) Wastewater Treatment Project, the McLoughlin Point facility treats wastewater to a tertiary level before discharging it through a new outfall extending approximately 2 km into the ocean.
In addition to the McLoughlin Point facility, the CRD’s Wastewater Treatment Project entailed the design and construction of the Residuals Treatment Facility to convert wastewater solids into a highly treated product for beneficial reuse as well as major upgrades to the existing collection system to reduce wet weather overflows. With these components in place, the ambitious Wastewater Treatment Project is significantly reducing the discharge of pollutants to the environment and employing advanced approaches to maximize resource recovery and improve sustainability.
The days of ‘preliminary treatment only’
Located at the entrance of the Victoria Harbour, the McLoughlin Point WWTP treats wastewater from the municipalities of Victoria, Esquimalt, Saanich, Oak Bay, View Royal, Colwood, and Langford as well as the Esquimalt and Songhees nations. Before December, wastewater underwent preliminary treatment at either the Clover Point Pump Station or the Macaulay Point Pump Station and then was discharged by means of outfalls into the Strait of Juan de Fuca (see project map).
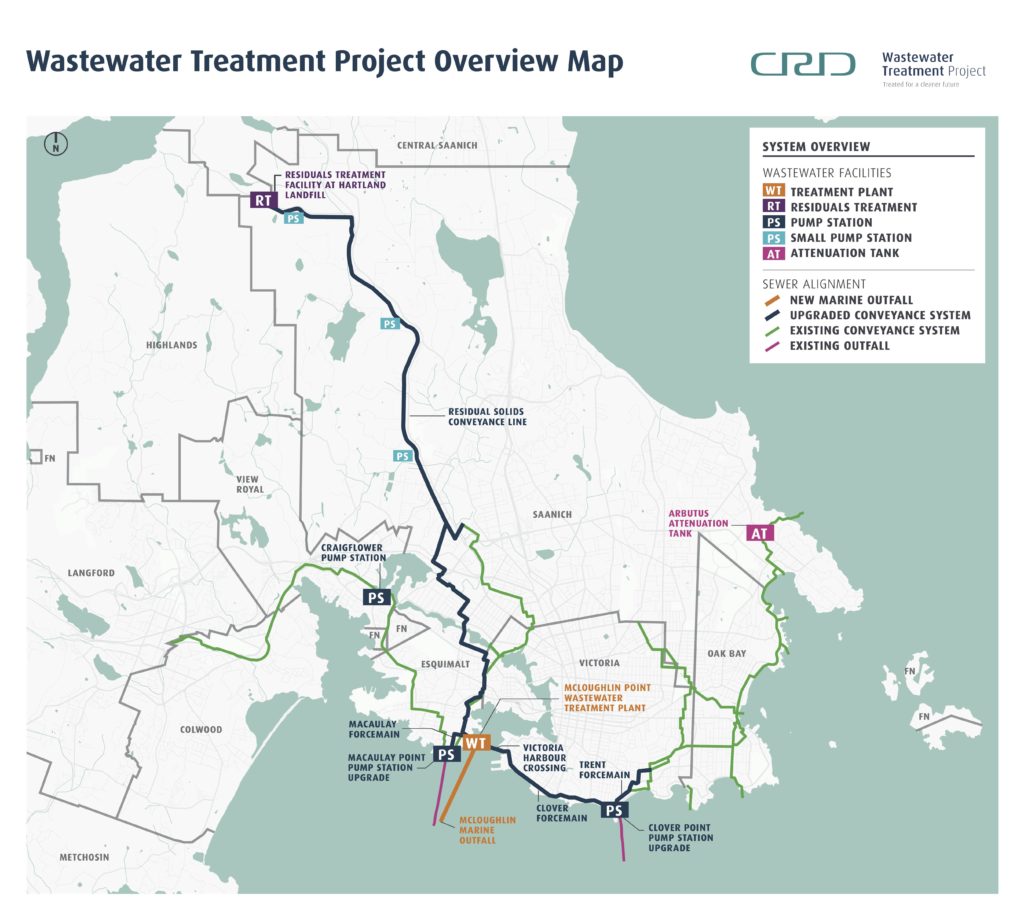
At the two pump stations, wastewater received “preliminary treatment only,” says Elizabeth Scott, the deputy project director for the CRD. The raw sewage passed through 6 mm screens before being pumped through outfalls into the ocean. During wet weather events, infiltration and inflow into the area’s collection system resulted in sewer overflows that were discharged from shorter outfalls without undergoing any treatment at all, Scott says.
Well beyond secondary treatment
A regional government entity that provides such services as drinking water, wastewater treatment, solid waste handling, and parks and recreation, the CRD faced a deadline of Dec. 31, 2020, to begin operating the new WWTP. In 2017, the district hired Harbour Resource Partners — a consortium comprising AECOM Canada and Graham Infrastructure, a division of Graham Construction & Engineering Inc. — to deliver the treatment plant, a new pipeline beneath Victoria Harbour, and the new marine outfall by means of a design-build-finance approach.
A key design challenge concerned the small site that had been selected for the treatment facility. “One of the interesting design factors for us is that the plant site is actually pretty constrained for a facility that’s going to treat wastewater from the population base,” Scott says. “That drove some of the selection of the treatment technologies.”
For example, secondary treatment consists of moving bed biofilm reactor tanks followed by biological aerated filter units. These systems, both of which house media in an aerated environment to promote biofilm growth, require less space than traditional secondary aeration units. For tertiary treatment, wastewater then passes through fabric disc filters that have 5 µm openings.
This last step “reduces many of the remaining pharmaceuticals, hormones, microplastics, and other contaminants,” Scott says. “The key benefit of the tertiary (treatment) is that it removes contaminants of emerging concern that may not be regulated today but could be in the future.”
To date, the treatment plant has exceeded its regulatory requirements handily, particularly with regard to the key parameters of total suspended solids and five-day carbonaceous biochemical oxygen demand. “The provincial regulatory requirements were to not exceed 45 mg/L for each,” Scott says. Canadian regulations at the federal level, meanwhile, require that the facility comply with a monthly average of less than 25 mg/L for both total suspended solids and carbonaceous biochemical oxygen demand. “We’re actually operating the plant such that we can achieve a monthly average of 10 mg/L” for each of the two parameters, Scott says.
Good neighbor practices
Because the WWTP is located in an urban setting, “odor control was an important consideration for us,” Scott says. “One of the design criteria was that there be no detectable odors by residents. The way that was met was with a state-of-the-art odor-control system complete with a 24-hour monitoring system.”
As a first step, “all of the treatment processing tanks are covered and operate under negative air pressure,” Scott explains. In this way, air leaves the primary treatment tanks and enters a two-stage odor-control system. “We have a biotrickling filter system that uses bacterial growth to break down odorous compounds, followed by an activated carbon system that adsorbs most of the remaining compounds,” she says. Similarly, the less odorous air from the secondary treatment reactors undergoes treatment in an activated carbon system.
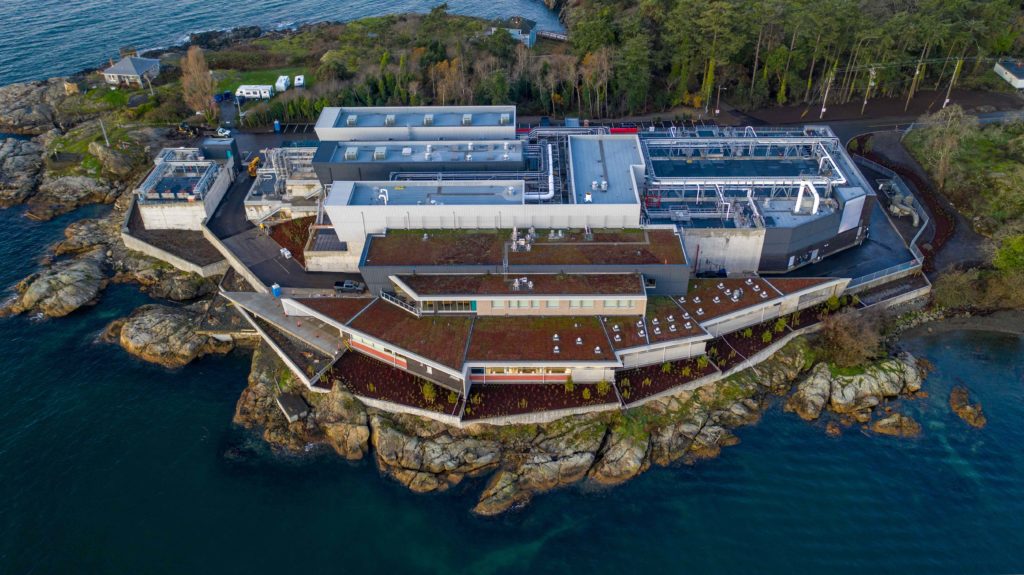
Sustainability also was a key design criterion. To this end, the operations and maintenance facility at the WWTP was built to comply with the gold rating level of the Leadership in Energy and Environmental Design standards developed by the U.S. Green Building Council. Among the factors that helped achieve the gold rating is heat recovery. “Effluent passes through heat exchangers,” Scott says. “They remove heat from the wastewater, which is used to heat the buildings at the plant.” Use of the heat exchangers “obviously reduces the amount of electricity that we need to use for heating,” she says.
Another key factor in achieving the gold rating involved extensive use of green roofs as a means of managing stormwater on-site. Approximately 80 percent of the operations and maintenance building’s 1,600 sq m rooftop consists of green roof, Scott says.
A crab-friendly outfall
Treated effluent is discharged from the marine outfall at a depth of 60 m. Made of high-density polyethylene, the outfall is held in place by means of 350 concrete ballast weights, each of which weighs approximately 11,400 kg and is spaced 4 to 6 m apart.
As part of efforts to comply with environmental requirements, the CRD installed 20 small steel bridges, known as “crab ramps,” to facilitate the movement of crabs and other aquatic species over the outfall. Attached to the anchor weights, the bridges “act as ramps over the outfall to ensure that crab movement isn’t restricted by the presence of the outfall,” Scott says. “We have already seen various forms of sea life using (the ramps), including Dungeness and red rock crabs,” she notes.
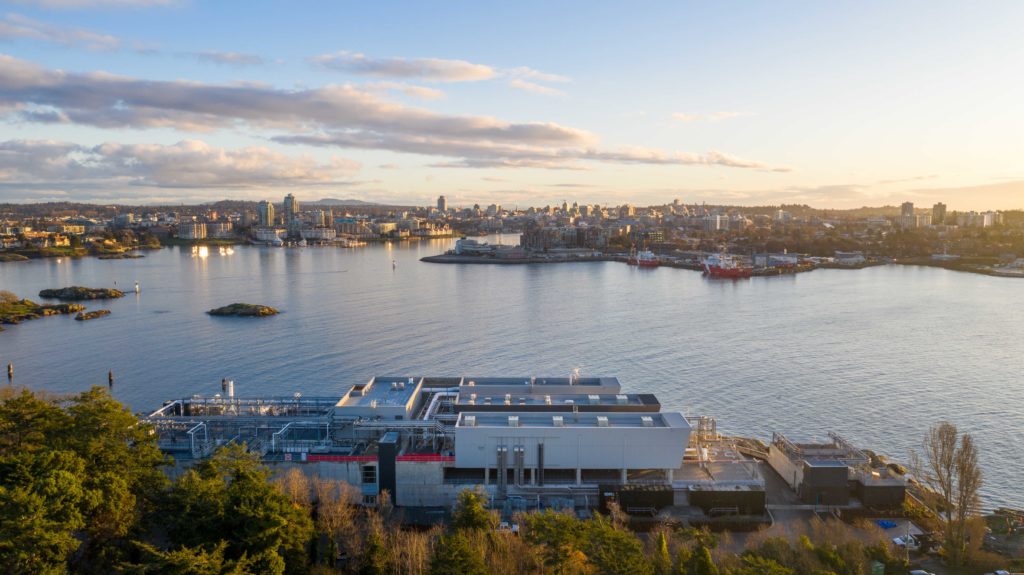
In 2018, Harbour Resource Partners completed construction of a pipeline beneath Victoria Harbour to enable the Clover Point Pump Station to convey flows to the McLoughlin Point WWTP. The 1.1 m diameter steel pipeline was installed within a 1 km long tunnel to protect it against damage from ships or anchors in the busy harbor.
Turning solids into fuel
The limited space at the site of the WWTP left no room for solids handling. Therefore, the CRD opted to construct its Residuals Treatment Facility approximately 19 km to the north, at the site of the district’s Hartland Landfill. The Harbour Resource Management Group — a consortium comprising Bird Construction Inc., Maple Reinders PPP Ltd., and Synagro Capital — delivered the facility by means of a design-build-finance-operations-maintenance approach. Under the terms of the agreement, Harbour Resource Management Group will operate and maintain the facility for 20 years.
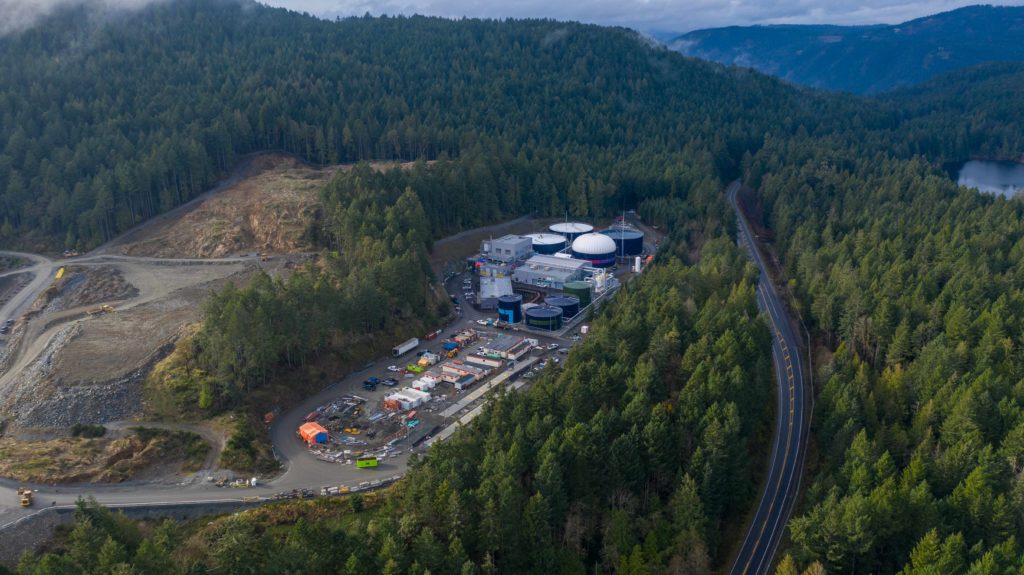
The facility, which can treat more than 14,000 dry tonnes of residuals annually, uses anaerobic digesters to break down solids, followed by centrifuges to conduct dewatering. The dewatered solids then are heated in a fluidized bed dryer at approximately 220 degrees Celsius to create dried pellets that meet British Columbia’s requirements for Class A biosolids — that is, biosolids that have undergone the most stringent treatment and have the fewest restrictions on their use.
For the first five years of the facility’s operation, the finished pellets will be used as an alternative fuel source at cement manufacturing plants, Scott says. In this manner, the pellets “will displace nonrenewable fuel sources,” she notes. Similarly, biogas produced by the anaerobic digesters is collected and used to fuel the centrifuges and dryer. “The facility is thermally self-sufficient,” Scott notes. “We just require electricity for the lights and the pumps.”
Additional improvements
A new 250 mm diameter pipeline, equipped with three pump stations, was constructed to convey solids from the McLoughlin Point WWTP to the Residuals Treatment Facility. Meanwhile, liquid removed during the residuals treatment process is returned to the head of the WWTP by means of a new 12 km long, 300 mm diameter pipeline. The pipeline sends these flows to a small pump station, which then conveys the liquid to the existing collection system that serves the WWTP.
Additional system improvements included upgrades of the Clover Point and Macaulay Point pump stations as well as force mains leading from the facilities to the WWTP. However, both pump stations retain the ability to discharge to the ocean via their outfalls in the event of excessive wet weather events. Kenaidan Contracting Ltd. designed and built the new Clover Point and Macaulay Point pump stations.
Stantec conducted the indicative design for the remaining improvements to the collection system. “We had different consultants develop that indicative design through to final design,” Scott says. Among the improvements was the new 1.9 km long Trent Force Main, which upon completion this spring will deliver flows to the Clover Point Pump Station. Another such improvement is the Arbutus Attenuation Tank, which will increase system capacity during wet weather events. Also to be completed this spring, the 5,000 cu m concrete tank will store flows during storm events and then return flows to the conveyance system after capacity has returned.